Engineers create ‘soft’ robots that could move like millipedes or go inside people
New techniques have been used to make a robot hand, a flapping fish tail, and a coil that can retrieve a ball
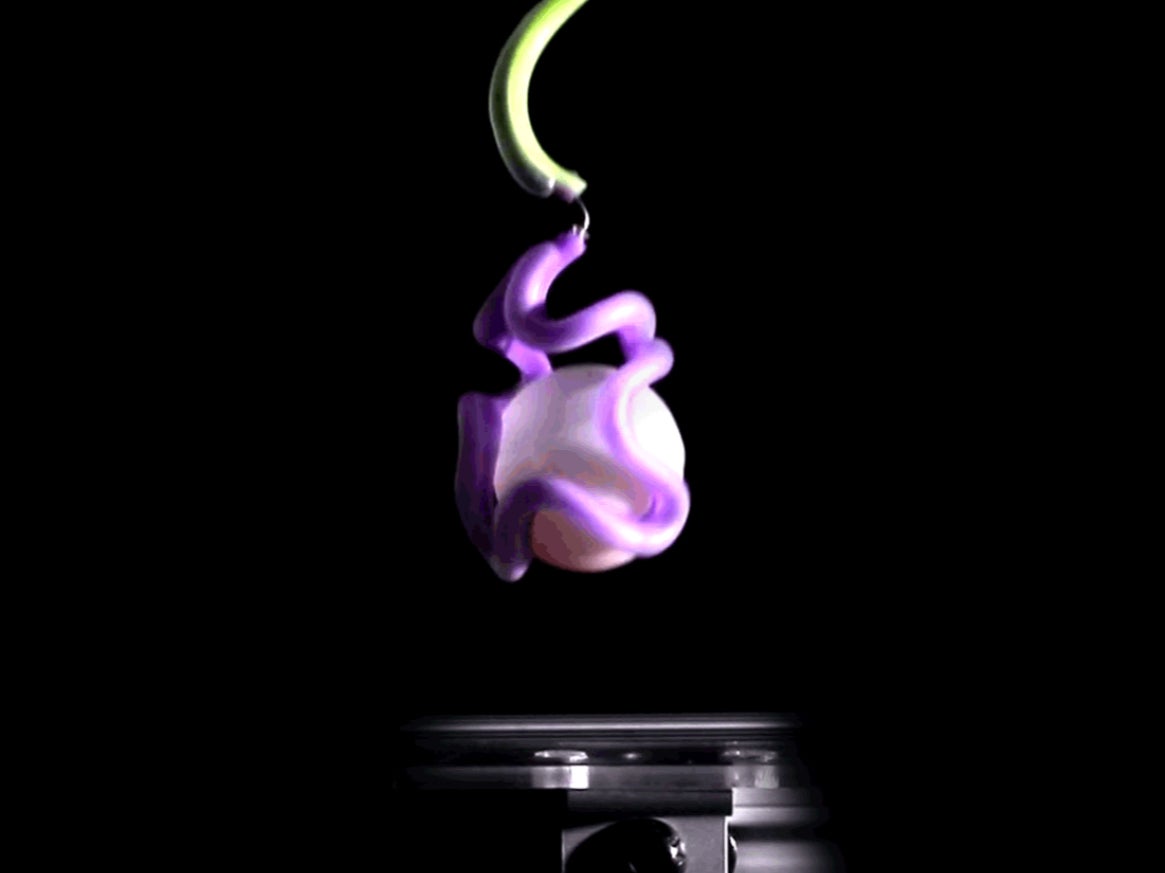
Your support helps us to tell the story
From reproductive rights to climate change to Big Tech, The Independent is on the ground when the story is developing. Whether it's investigating the financials of Elon Musk's pro-Trump PAC or producing our latest documentary, 'The A Word', which shines a light on the American women fighting for reproductive rights, we know how important it is to parse out the facts from the messaging.
At such a critical moment in US history, we need reporters on the ground. Your donation allows us to keep sending journalists to speak to both sides of the story.
The Independent is trusted by Americans across the entire political spectrum. And unlike many other quality news outlets, we choose not to lock Americans out of our reporting and analysis with paywalls. We believe quality journalism should be available to everyone, paid for by those who can afford it.
Your support makes all the difference.Scientists have found a way to make ‘soft robots’ using balloons that change shape when inflated with air.
This new technology has been used to create a robot with a gripping hand, a flapping fish tail, and a moving coil that can be used to retrieve a ball.
In contrast to conventional rigid robots, these soft robots are “naturally geared to interact with the soft stuff, like humans or tomatoes”, assistant professor of chemical and biological engineering at Pierre-Thomas Brun at Princeton says.
This could make them significantly more useful for harvesting food, taking items off a conveyor belt, or providing health care – as part of wearable exosuits or under-the-skin devices that could help people with heart issues.
The robots are built by injecting bubbles into a liquid polymer called elastomer which becomes rubbery when it solidifies, then inflating the device to make it bend and move. Gravity helps the bubble rise to the top as the elastomer reaches the bottom; once it has hardened, it can be removed from the mold and inflated.
Developing the robots is not an easy task; controlling how they stretch and deform through their actuators (components which control movement) is more challenging than with rigid robots due as they can potentially change in an infinite number of ways.
Factors such as the thickness of the elastomer coating, how quickly it settles, and how long it takes to harden all affect how the robot will move. These actuators can also be several metres long, with features as small as a human hair.
"If it’s allowed more time to drain before curing, the film at the top will be thinner. And the thinner the film, the more it will stretch when you inflate it and cause greater overall bending," Trevor Jones, a chemical and biological engineering researcher.
As well as air, the robots could also be activated using magnetism, electric currents, or changes in temperature and humidity. Predicting how these robots will work is done using a “simple equation that anyone can use”, researcher Etienne Jambon-Puillet says.
Currently, the researchers have created star-shaped hands that can grip a blackberry, a coiling muscle, and fingers that can curl up one by one. It is not foolproof, though. Bubble casting has only seen real success over a few metres of elastomer-filled tubing, and overinflation can cause it to pop.
"Failure is fairly catastrophic," Jones says.
The researchers hope to further develop these robots that will move together in sequential waves like a millipede, or which contract and relax from a single source akin to a human heart.
"We understand this problem at a physics level pretty strongly," said Jones. "So now the robotics can really be explored."
Join our commenting forum
Join thought-provoking conversations, follow other Independent readers and see their replies
Comments