‘I could see the chaos filtering down’: Former Boeing staffer blows whistle on planemaker’s practices
‘I wondered what was going on and why we were accepting substandard, incomplete work,’ says Douglas Dorsey, a former manufacturing engineer
Your support helps us to tell the story
From reproductive rights to climate change to Big Tech, The Independent is on the ground when the story is developing. Whether it's investigating the financials of Elon Musk's pro-Trump PAC or producing our latest documentary, 'The A Word', which shines a light on the American women fighting for reproductive rights, we know how important it is to parse out the facts from the messaging.
At such a critical moment in US history, we need reporters on the ground. Your donation allows us to keep sending journalists to speak to both sides of the story.
The Independent is trusted by Americans across the entire political spectrum. And unlike many other quality news outlets, we choose not to lock Americans out of our reporting and analysis with paywalls. We believe quality journalism should be available to everyone, paid for by those who can afford it.
Your support makes all the difference.A long-time Boeing staffer has spoken out about problematic outsourcing and manufacturing practices that began to become a “really big problem” for the planemaker.
Boeing’s reputation has been left shaken after a turbulent 2024, which saw an Alaska Airlines 737 Max door plug blow out mid-flight, 33,000 workers go on strike and dozens of whistleblowers speaking out about the quality of parts and manufacturing processes.
And just five days into 2025, an Etihad Airways Boeing 787-9 Dreamliner was forced to abort takeoff from Melbourne Airport in Australia due to “technical reasons,” the airline said.
Douglas Dorsey, from Hansville, Washington, worked as a manufacturing engineer at the embattled aerospace company from 1984 before retiring in 2017.
The Boeing “lifer” wrote in a Business Insider essay that he once had “blue blood running through my veins”.
But as Dorsey worked on the Boeing 777 and 787 Dreamliner across the 1990s and 2000s as more manufacturing was outsourced, he said things began to unravel, leading to “chaos” filtering down the chain of command and “substandard work” being accepted.
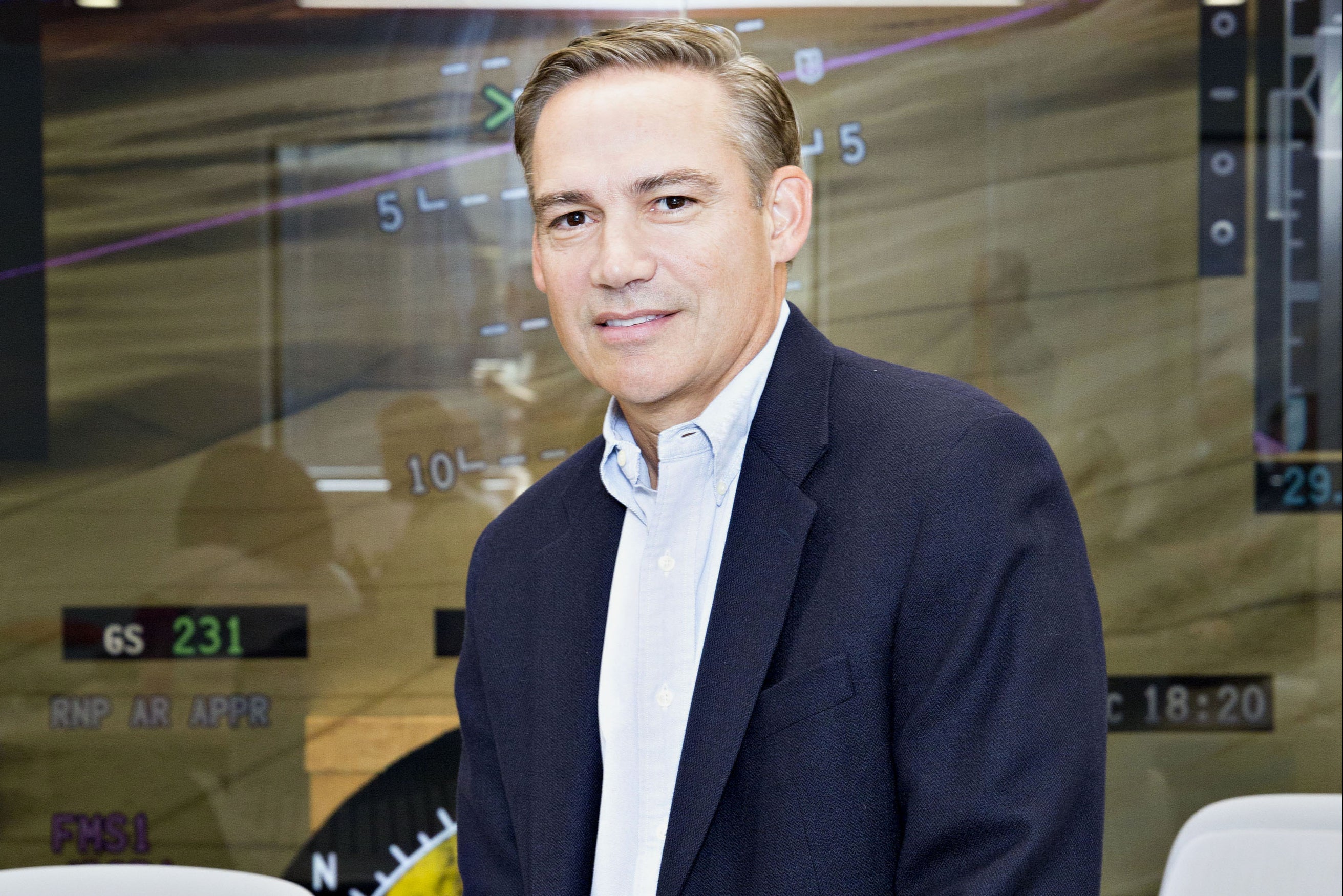
Within his first 10 years at the company – what Dorsey fondly recalled as the “good old days” – he said the chain of command was clear.
“There was no drama with executives, and we had confidence in those in command,” he said.
But in 1997, Dorsey said that upper management was thrown into disarray upon Boeing’s merger with McDonnell Douglas, a major American aerospace and defense company before the acquisition.
A broad swathe of leadership ranks were filled by McDonnell Douglas veterans – not Boeing executives – many of whom had backgrounds in finance rather than engineering.
It wasn’t until working on the Boeing 787 program in the 2000s, Dorsey said, where cracks really began to show in the outsourcing manufacturing tasks to suppliers.
“I noticed that outsourcing manufacturing tasks to suppliers became a really big problem for Boeing,” he said.
The Boeing veteran said that at the beginning of each new airplane program, management divided major sections of the aircraft among various subcontractors, suppliers, and risk-sharing partners.
To get planes in the sky more quickly, Boeing would have the risk-sharing partners deliver complete aircraft sections to the final assembly site, Dorsey said.
A suite of new executives and juggling the management of contractors led to more stilted communications and, subsequently, had a negative impact on production quality.
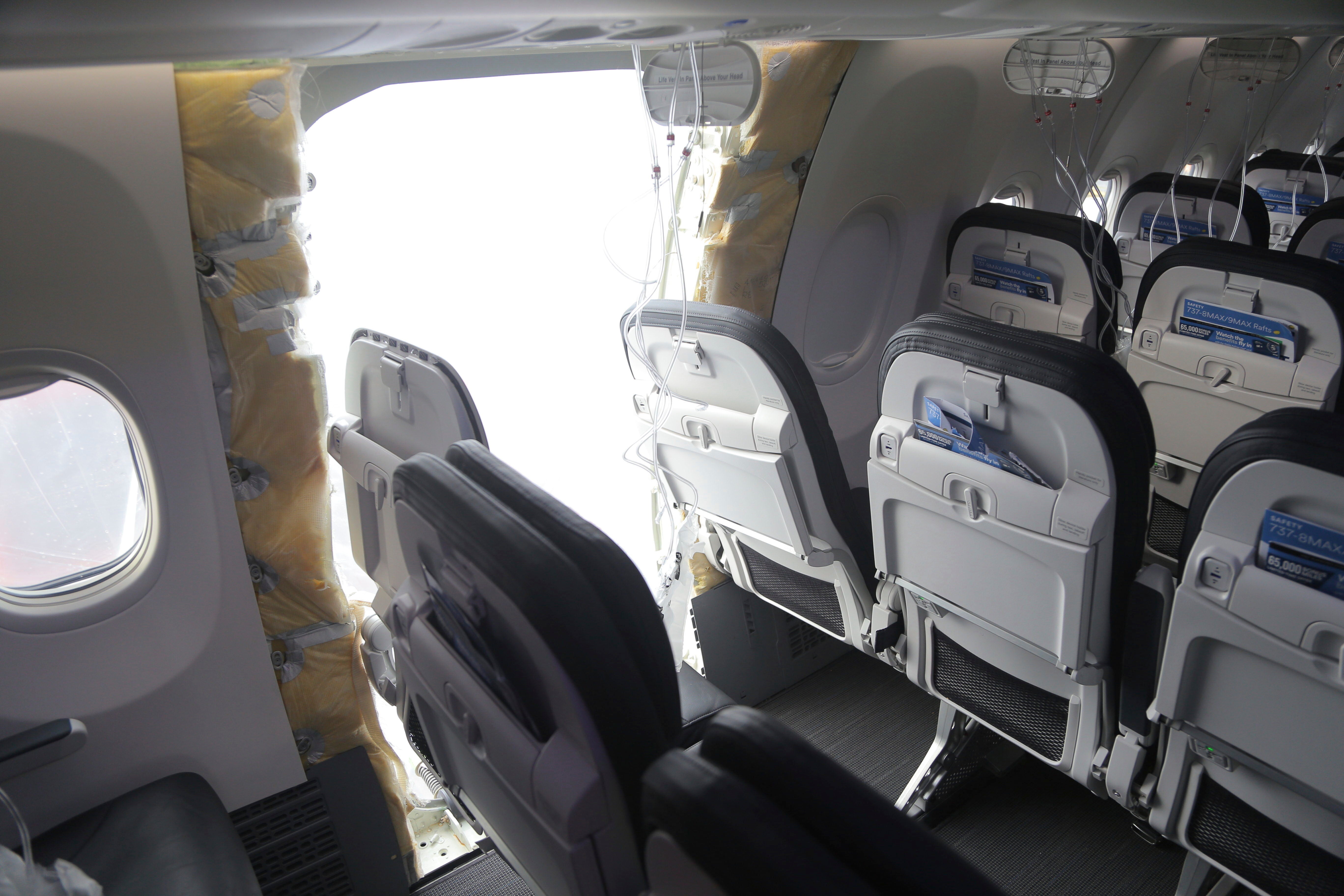
“When I worked on the shop floor, I saw the negative impacts of outsourcing to suppliers, such as slower production and delivering incomplete parts,” he said. “I spent much of my time on the program trying to accommodate parts that had a ‘non-conformance’ tag on them and had to be reworked and installed into the build.
“I wondered what was going on and why we were accepting substandard, incomplete work.”
Boeing executives failed to take note when employees working on the ground flagged problems and made suggestions about improving processes, Dorsey claimed.
“As an engineer, I wasn’t privy to the decisions going on in the upper chambers of management, but I could see the chaos filtering down,” he said. “It felt like the company wasn’t listening to its mechanics about how to improve processes.”
The 787 was ultimately delayed by three years, embarking on its first commercial flight in September 2011.
Despite his criticism, Kelly believes that CEO KellyOrtberg, who was appointed in August, may be able to steady the ship while helping Boeing overcome its PR problem.
“I see these actions as baby steps in the right direction. Kelly Ortberg, Boeing’s CEO, is trying to steer the company on a new course, but I think it’s going to take a long time,” he said.
In response to his scathing critique, a Boeing spokesperson shared remarks made by Ortberg in October 2024 with Business Insider.
At the time, Ortberg said: “Much has been written about how we got to where we are, but most also recognize that Boeing was once a benchmark for what good culture looks like. And I believe we can return to that legacy. I know culture change starts at the top. Our leaders, from me on down, need to be closely integrated with our business and the people who are doing the design and production of our products.
“We need to be on the factory floors, in the back shops, and in our engineering labs. We need to know what’s going on, not only with our products but with our people.”
The Independent has contacted Boeing for more information.
Join our commenting forum
Join thought-provoking conversations, follow other Independent readers and see their replies
Comments