Cracks in trains caused by excess movement and salt in the air – report
The withdrawal of Class 800 trains until additional safety checks were introduced led to a week of severe disruption to services in May last year.
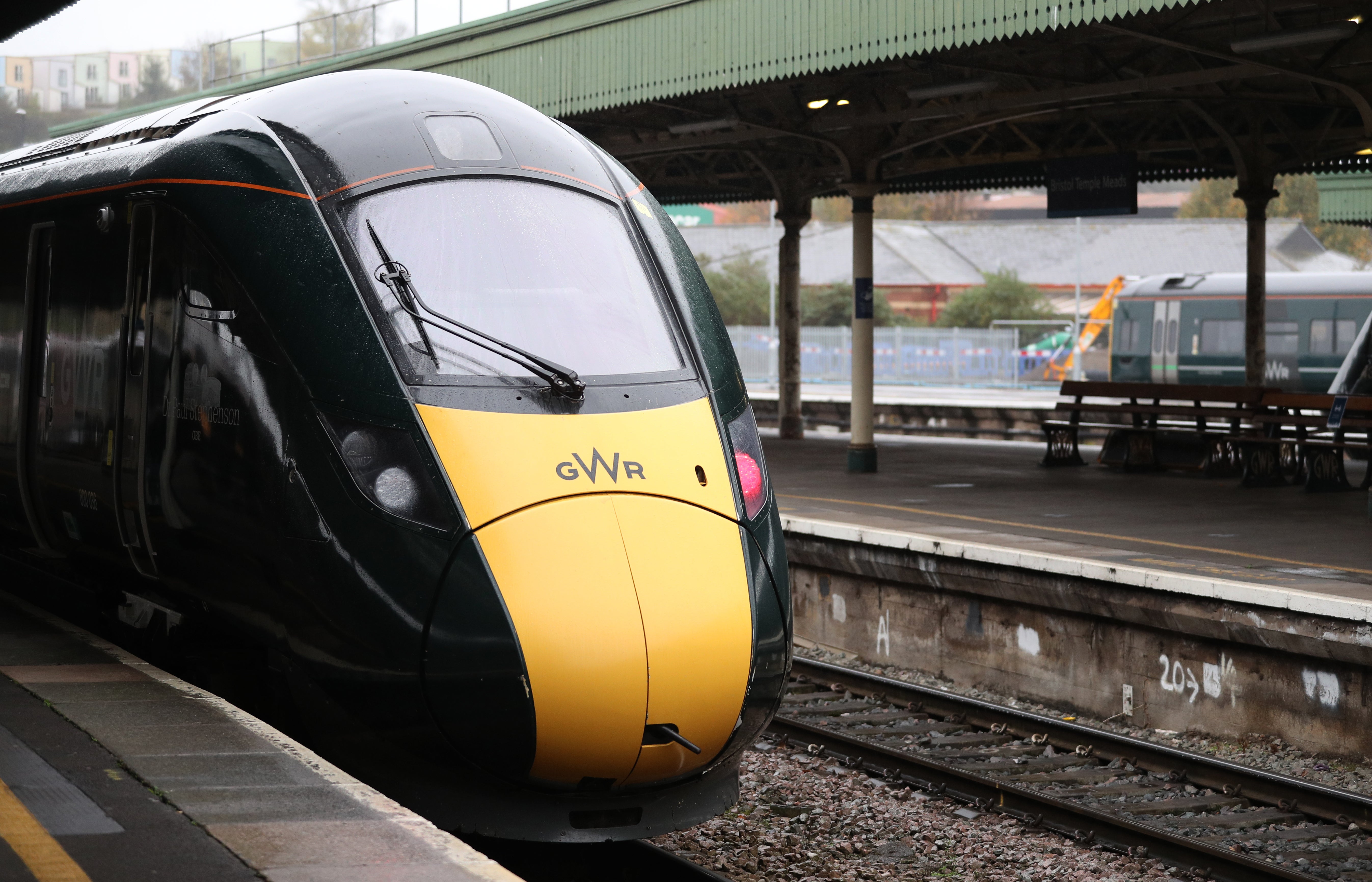
Your support helps us to tell the story
From reproductive rights to climate change to Big Tech, The Independent is on the ground when the story is developing. Whether it's investigating the financials of Elon Musk's pro-Trump PAC or producing our latest documentary, 'The A Word', which shines a light on the American women fighting for reproductive rights, we know how important it is to parse out the facts from the messaging.
At such a critical moment in US history, we need reporters on the ground. Your donation allows us to keep sending journalists to speak to both sides of the story.
The Independent is trusted by Americans across the entire political spectrum. And unlike many other quality news outlets, we choose not to lock Americans out of our reporting and analysis with paywalls. We believe quality journalism should be available to everyone, paid for by those who can afford it.
Your support makes all the difference.Cracks on trains discovered last year were caused by excess movement and aluminium corroded by salt in the air, an investigation has found.
Fatigue cracking in the area above the wheels of Hitachi-built Class 800 trains was a result of the rolling stock experiencing more movement than allowed in original designs, rail safety regulator the Office of Rail and Road (ORR) said.
It is not known for certain why this happened but potential factors identified include wheel wear – which is when the shape of wheels changes during use – and track design.
The ORR found cracks on lifting points – which allow carriages to be raised during maintenance work – resulted from the use of a particular type of aluminium which was corroded by salt in the air.
The withdrawal of Class 800 trains until additional safety checks were introduced led to a week of severe disruption to services last May.
Affected operators were Great Western Railway, London North Eastern Railway, TransPennine Express and Hull Trains.
Cracks were also found after examination of ScotRail’s Class 385 and Southeastern’s Class 395 trains.
The ORR said “stringent mitigation measures” such as regular inspections were put in place to allow trains to re-enter service “without passenger safety being compromised”.
The trains have “performed as specified” and “no safety failures” have been recorded.
Our review provides a clearer picture of the issue and we will continue our oversight to ensure work moves forward to agree the permanent solution and our recommendations are acted on
Recommendations issued by the regulator include the rail industry collaborating to evaluate whether standards for train design, manufacture and maintenance take into account pressures created by train movement on Britain’s railways.
It urged Hitachi to conduct a formal review of its welding processes, and for train designers to consider what steps should be taken to ensure protection of structures when 7000 series aluminium components are used, as they were in building Class 800 trains.
The report also called on the industry to develop a process for responding to similar “crisis events” in the future.
Hitachi and its partners are preparing to launch a major programme of work to repair 1,247 Class 800 trains, and 487 of its Class 385 and 395 trains.
This is expected to take place over the next six years to minimise the number of trains taken out of service at any one time.
The timeframe includes three years for repairs and three years for preventative activities.
ORR’s HM Chief Inspector of Railways Ian Prosser said: “With our oversight, Hitachi Rail and operators have put in place robust plans to make sure the right safety issues are being managed following the initial discovery of cracks on the trains, which have allowed trains to re-enter service.
“Safety remains the number one priority. Our review provides a clearer picture of the issue and we will continue our oversight to ensure work moves forward to agree the permanent solution and our recommendations are acted on.
“It is important that the whole industry works together to learn lessons from what has happened and our recommendations will help with that.”
A Hitachi Rail spokesman said: “The ORR’s report identifies that all Hitachi trains meet relevant standards and that we took the appropriate action to prioritise safety and maintain train availability.
“The report also provides a detailed account of the tireless work to simultaneously keep trains running safely while working towards the long-term solutions.
“The proposed engineering solutions outlined in the report are currently being reviewed by all partners.
“We are working together to finalise the plan for their implementation, while always prioritising safety and train availability to support consistent passenger services.”