Royal Mint opens new factory to recover gold from e-waste
Up to 4,000 tonnes of Printed Circuit Boards from items like laptops and TVs will be processed by The Royal Mint per year.
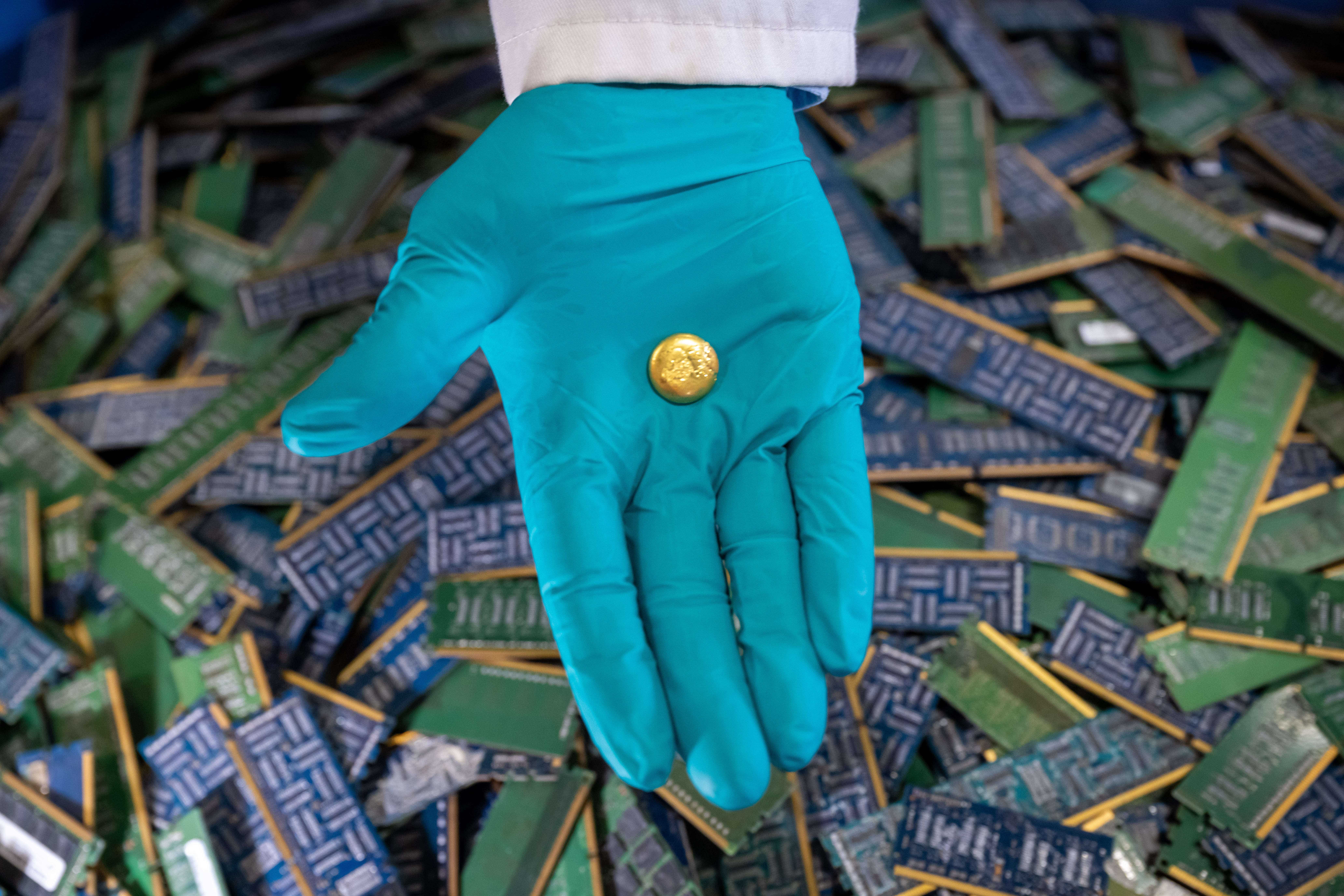
Your support helps us to tell the story
From reproductive rights to climate change to Big Tech, The Independent is on the ground when the story is developing. Whether it's investigating the financials of Elon Musk's pro-Trump PAC or producing our latest documentary, 'The A Word', which shines a light on the American women fighting for reproductive rights, we know how important it is to parse out the facts from the messaging.
At such a critical moment in US history, we need reporters on the ground. Your donation allows us to keep sending journalists to speak to both sides of the story.
The Independent is trusted by Americans across the entire political spectrum. And unlike many other quality news outlets, we choose not to lock Americans out of our reporting and analysis with paywalls. We believe quality journalism should be available to everyone, paid for by those who can afford it.
Your support makes all the difference.The Royal Mint has opened a new factory to remove gold from old computers and phones and turn it into jewellery and collectables.
The facility provides a sustainable source of precious metals and reduces reliance on mining.
Up to 4,000 tonnes of printed circuit boards (PCBs) from e-waste like old laptops and TVs will be processed by The Royal Mint per year.
It takes around 600 mobile phones to create one of the rings from the Mint’s 886 collection, weighing approximately 7.5g – similar to the weight of a £1 coin.
Some 4,000 tonnes of circuit boards contain half a tonne of gold, 1,000 tonnes of copper, 2.5 tonnes of silver and 50kg to 60kg of palladium.
On average, one tonne of circuit boards produces 165gm of gold, equating to around £9k.
Mark Loveridge, business unit director at Precious Metals Recovery, told the PA News Agency the factory processes were a “world first”, adding that the Mint is very good at taking things “from a beaker to an industrial scale”.
He also said: “If we look at e-waste generated the UK is the second worst offender in terms of the amount we produce per capita.
“It’s the equivalent of about 25 kilos a person. And that’s the equivalent to about a 50-inch TV, just to give you an idea in terms of what that kind of translates into.
“We all have our jar at home where we put our coins into. It’s the same with our electronic devices.
“You have probably got a couple of mobile phones sat in a drawer and TV in the back bedroom or the garage or something that needs to come back into that supply chain so it can be recycled and those materials recovered.”
The silver and gold are used by the official maker of British coins to produce jewellery and commemorative coins.
The non-precious metal that is recovered (copper, tin, steel, aluminium) is sent to other companies as a raw material to turn them into products such as sheets/bars/rods to manufacture new products.
The idea is that recovered, high-purity gold will reduce the dependence on traditional mining activity and encourage more sustainable industry practices.
As things stand, The Royal Mint receives the circuit boards, which are then processed in a newly built specialised plant, which separates all the components and metals.
The Royal Mint is transforming for the future, and the opening of our Precious Metals Recovery factory marks a pivotal step in our journey
The pieces containing the gold are then sent on to a second facility on the South Wales site, which uses world-first patented chemistry from Canadian cleantech company Excir to remove the metal.
Unlike other gold extraction processes that require extremely high temperatures, and take a lot of time, the new process at the Mint uses a washing machine-style spinning drum that washes the gold-containing parts in a special acid mix that dissolves the precious metal in just four minutes.
It also does this at temperatures of just 20C to 25C, using a lot less energy than other gold extraction methods.
The factory is powered by electricity, and there are wind turbines and a solar farm on site.
Everything from the process is recycled, or reused, from the plastic on the circuit boards to the acid used to dissolve the gold.
Anne Jessopp, chief executive at The Royal Mint, said: “The Royal Mint is transforming for the future, and the opening of our Precious Metals Recovery factory marks a pivotal step in our journey.
“We are not only preserving finite precious metals for future generations, but we are also preserving the expert craftsmanship.
“The Royal Mint is famous for creating new jobs and reskilling opportunities for our employees.
“We have ambitious plans, and I am proud that we are safeguarding The Royal Mint for another 1,100 years.”
As well as recycling the circuit boards it receives, The Royal Mint is also working towards receiving the entire items – computers, mobile phones, server equipment – so it can be involved in the full process.