Spatial computing: the next frontier of industrial efficiency
THE ARTICLES ON THESE PAGES ARE PRODUCED BY BUSINESS REPORTER, WHICH TAKES SOLE RESPONSIBILITY FOR THE CONTENTS
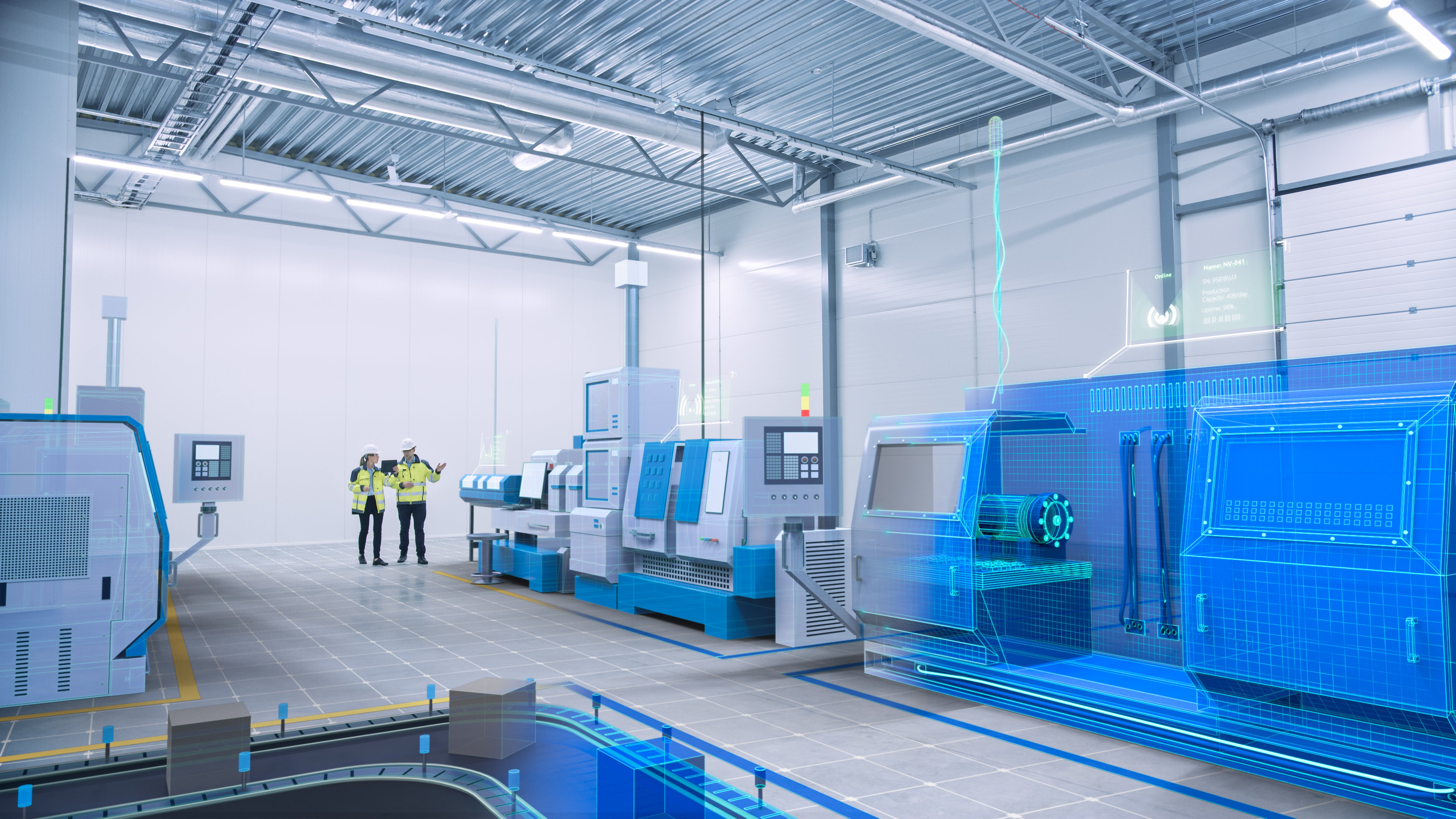
Spatial computing represents the logical next step in digital transformation for manufacturers looking to take worksite optimisation to a whole new level.
Smart factories are about to get even smarter. With the adoption of spatial computing – the digitisation of spatial relationships between machines, people and objects in order to identify their precise location and movements within a 3D space – industrial companies have an opportunity to take the optimisation of worksites to a whole new level.
To understand the scale of that opportunity, let’s first take a step back. Over the past decade, manufacturers have been able to reach new levels of efficiency through industrial internet of things (IIoT) programmes. These have equipped factory-floor machinery with smart sensors able to report on their status and usage and receive instructions remotely.
These connected operations have led to far greater insight into how facilities are running. In turn, companies have been able to make significant strides in terms of maximising revenue, reducing costs and improving quality – but the current benefits only extend so far, because IIoT still lacks important spatial information.
In short, traditional IIoT suffers from blind spots when it comes to the physical execution of processes in a 3D environment. When something goes wrong, often a worker must be sent out to diagnose the bottleneck – whether that’s an equipment malfunction, a colleague taking longer than usual to complete a task, or a misplaced pallet at one end of the production line. This relies on that worker being able to deduce the nature of the problem and put it right, a process that can be haphazard, error-prone and painstakingly slow.
Eyes on the ground
Over the next decade, spatial computing promises to tackle these blind spots, providing smart factories and other industrial workplaces with more accurate, non-human “eyes on the ground”.
The term “spatial computing” was defined by MIT Media Lab alumni Simon Greenwold in 2003, but it’s only in recent years that new technologies have made his futuristic vision possible. These include artificial intelligence (AI) and machine learning; camera sensors and computer vision technologies to track environments; IIoT to monitor and control products and assets; and augmented reality (AR) to provide the human user interface.
Spatially improved e-resolution cameras and AI in particular are opening up completely new applications. New camera technologies don’t just capture two dimensions; they also measure distances between machines, people and objects. When you can link the 3D images of multiple cameras and analyse the findings, it’s entirely possible to create far more comprehensive, real-time simulations of reality. The result is a “digital twin” of an entire factory, which can be monitored and controlled by interdisciplinary working groups, collaborating globally and remotely, as if they were all stood together on the factory floor.
If that vision sounds wildly improbable, it’s important to recognise that spatial computing is already hard at work today. If you’ve ever impatiently tracked the arrival of the next metro train on a passenger information screen or hungrily monitored the journey of your food delivery from a local restaurant to your doorstep, you’ve seen it at work. Spatial computing is already seen in the highly automated warehouses of e-commerce giants, where it’s used to orchestrate the rapid collection of specific goods from miles of shelving by automated guided vehicles (AGVs) in the most efficient way possible to meet customer expectations of next-day delivery.
But the potential use cases for spatial computing are far broader, especially in other industrial settings. In short, when a manufacturing company can achieve better oversight of the interactions and movements of every machine, person and object involved in a process, they will have the information they need to resolve any inefficiencies they identify in time, motion and use of space.
Human empowerment
That’s good news for bosses and their teams. Today, many managers rely on manual time and motion studies to optimise the work of employees – but according to a study by global management consulting firm Kearney, 43 per cent say they’re not confident in the findings these yield. Leveraging spatial computing analytics for continuous process improvement can more accurately and readily identify worker and production bottlenecks than previous methods. Spatial “heat maps”, for example, will give new clues into the time spent by a worker in a particular location at a particular stage in a workflow and what routes around the factory are used most frequently.
For workers, meanwhile, spatial computing connects them as a consumer and provider to the digital ecosystem that surrounds them. It can pinpoint for them, for example, where an error occurred on the shop floor and identify the best way to reach the trouble spot.
By analysing how employees perform on various tasks, it’s possible to identify the types of work where they perform best and then deploy them on tasks that match their particular skills and physical attributes. I like to think of these workers as “industrial athletes”, empowered to achieve their best work in ways that are more efficient, and safer, too.
It’s also a great opportunity for manufacturing companies to tackle their persistent skills gaps, through the training and reskilling of workers and by attracting younger recruits looking to forge careers in advanced, technology-driven environments. Spatial computing, for example, might be used to enable a human operator to reprogramme a production-line robot to perform a new task or designate waypoints for an AGV to carry a heavy load across a factory. With a shared understanding of the space and events happening around them, humans and machines can collaborate more harmoniously.
Look to the future
The impact of Covid-19 on the manufacturing industry has been huge, with many factories worldwide hit by closures and most others having to tailor operations and activities to suit reduced workforces, obliged to self-distance. In many cases, the remote monitoring/management capabilities delivered by previous digital transformation projects have paid dividends and many manufacturers are now inclined to double down on these investments. Spatial computing will take remote management up a notch, enabling companies to control and manage a broader scope of production line activities from a wider variety of locations.
In that sense, then, spatial computing is a logical step forward for efficiency-hungry industrial companies already on their digital transformation journeys. It’s an opportunity to create a workplace environment just as finely tuned as the processes conducted within it.
For more information, please visit www.ptc.com/en
Originally published on Business Reporter