Brick by brick, the UK construction sector is moving towards its net zero goals
THE ARTICLES ON THESE PAGES ARE PRODUCED BY BUSINESS REPORTER, WHICH TAKES SOLE RESPONSIBILITY FOR THE CONTENTS
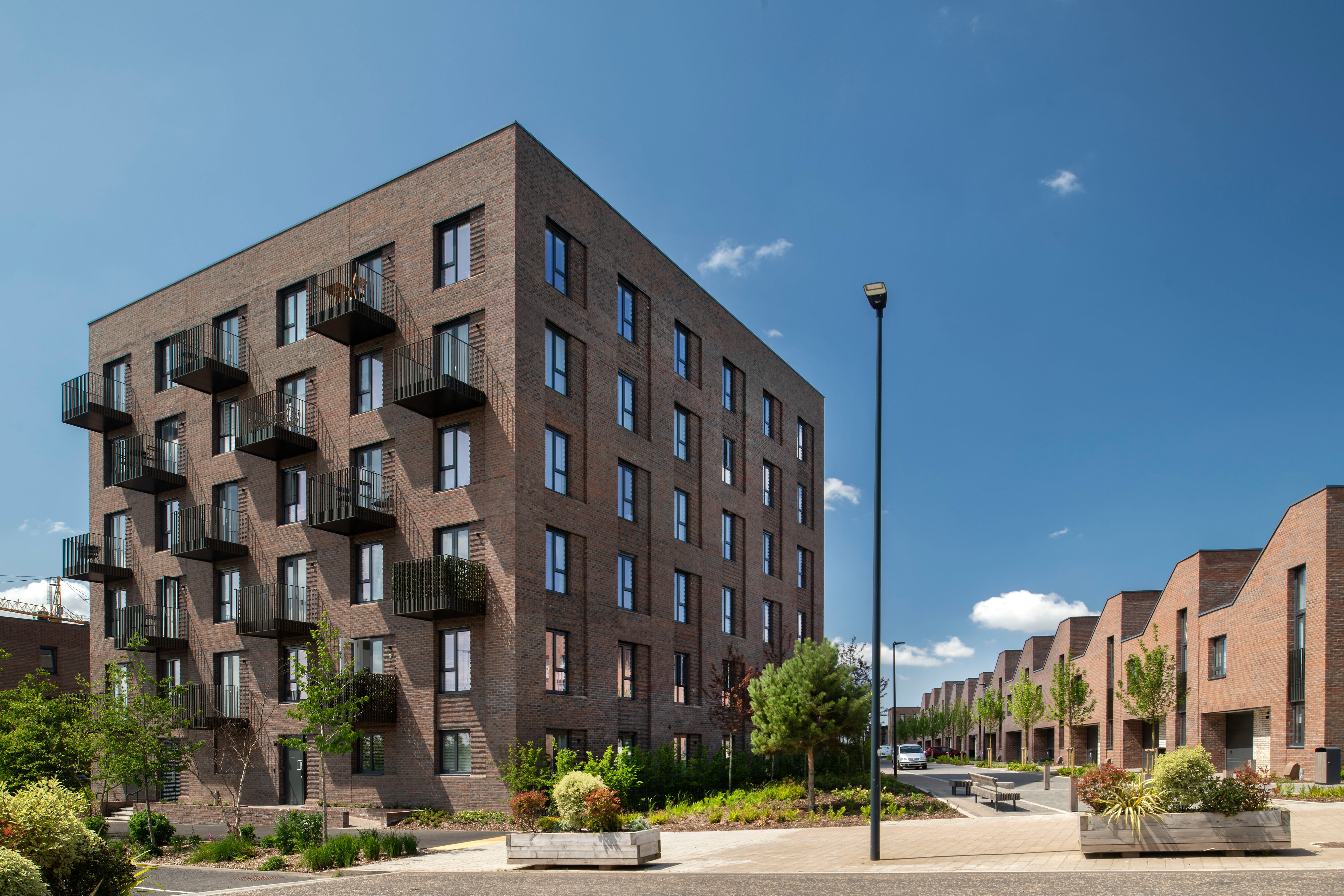

Michelmersh is a Business Reporter client.
Clay bricks have been in use for 9,000 years. The earliest known traces – found near the ancient city of Jericho, and dating from barely a millennium and a half after the end of the last ice age – are remarkably similar to modern bricks: made of mud clay, and formed into rectangular, stackable blocks.
It’s a timeless design. The fact that today’s bricks have barely changed from those of yesteryear is evidence of their enduring appeal – they are aesthetically pleasing, they store heat well, and they are durable. The fact that archaeologists were even able to discover remnants from so long ago shows just how long lasting these cuboids of compacted clay are.
In the conversation about climate-friendly building materials, however, bricks tend to be overlooked in favour of new innovations. This is puzzling. While many materials lose their integrity over time, bricks last centuries. They can be reused and recycled many times over.
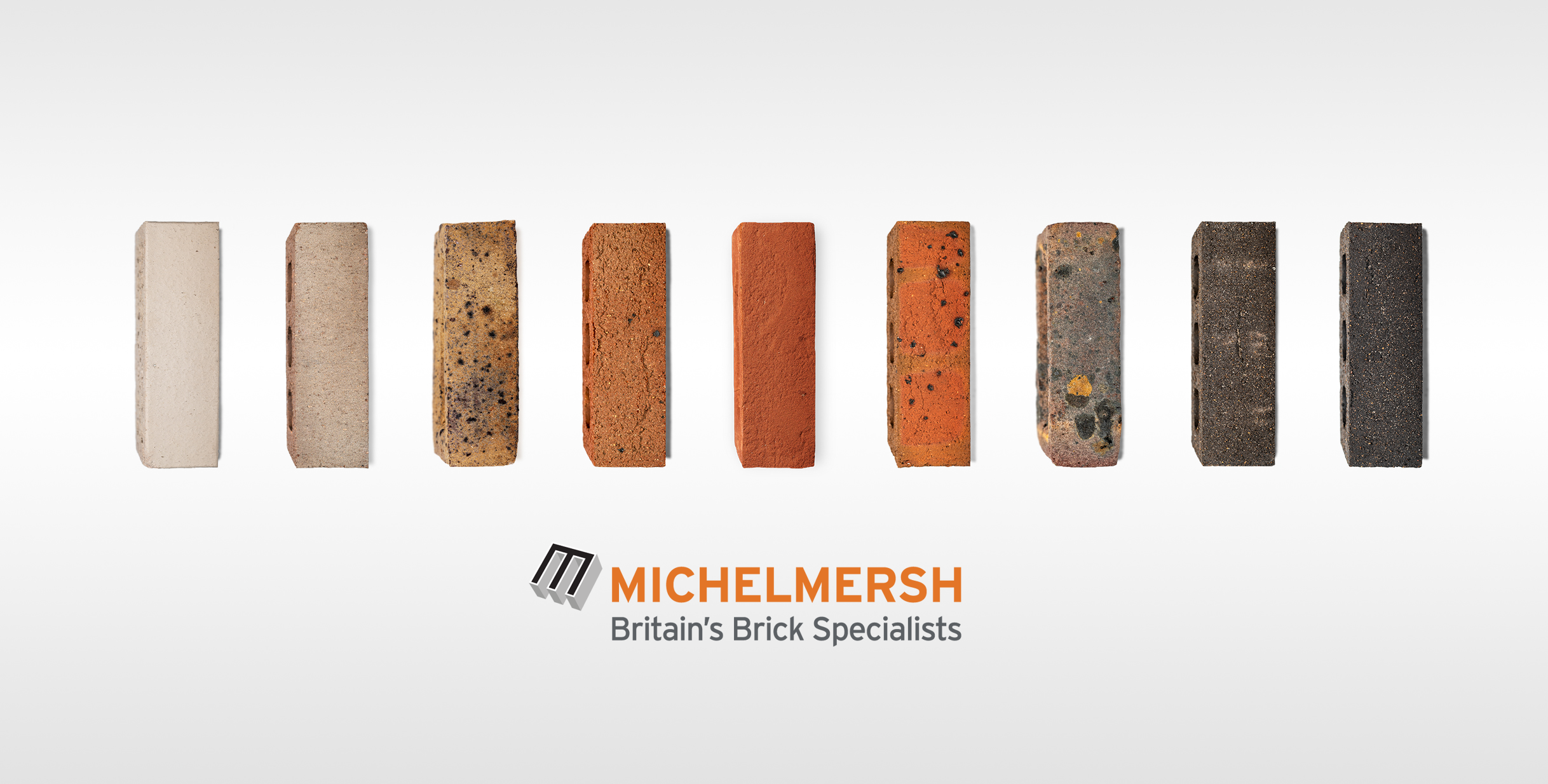
Moreover, unlike other construction materials, clay is a natural product with very low operational carbon output or maintenance over its whole life.
And if the clay can be sourced close to where the bricks are manufactured, then emissions from production are even lower.
Using British materials and labour
Michelmersh turns out more than 120 million clay bricks and pavers each year. More than 85 per cent of all its raw materials are sourced from within 2.5 kilometres of its factory sites, including 100 percent of its clay. Although it delivers nationally, most of its UK products are supplied locally – in fact most of its UK products travel on average 60 miles from factory to site.
The company’s location in West Sussex is a fitting one: archaeological digs there several decades ago uncovered a trove of Roman ceramics, meaning that Michelmersh is continuing an age-old tradition of using nearby natural resources to create sustainable, long-lasting building materials.
Using British materials and employing locally has been central to the company’s sustainable business model since it began its operations under the Michelmersh Group name in 1997. So too has its advocacy for building designers, architects and construction firms to design and build our architectural landscape to last longer.
“Real sustainability is understanding the full and lasting impact of our design choices and reducing the carbon footprint over the building’s entire lifetime, from cradle to grave,” says Sarah Le Gresley, Innovation Director for Michelmersh.
“Durable products with extensive longevity, such as clay brick, will prolong the expected life of a building, resulting in a lower carbon footprint for every year of use. Clay bricks can be reused and recycled, thereby further extending the usable life of the product and benefiting multiple generations.
“This is why we encourage architects and house builders to think longer.”
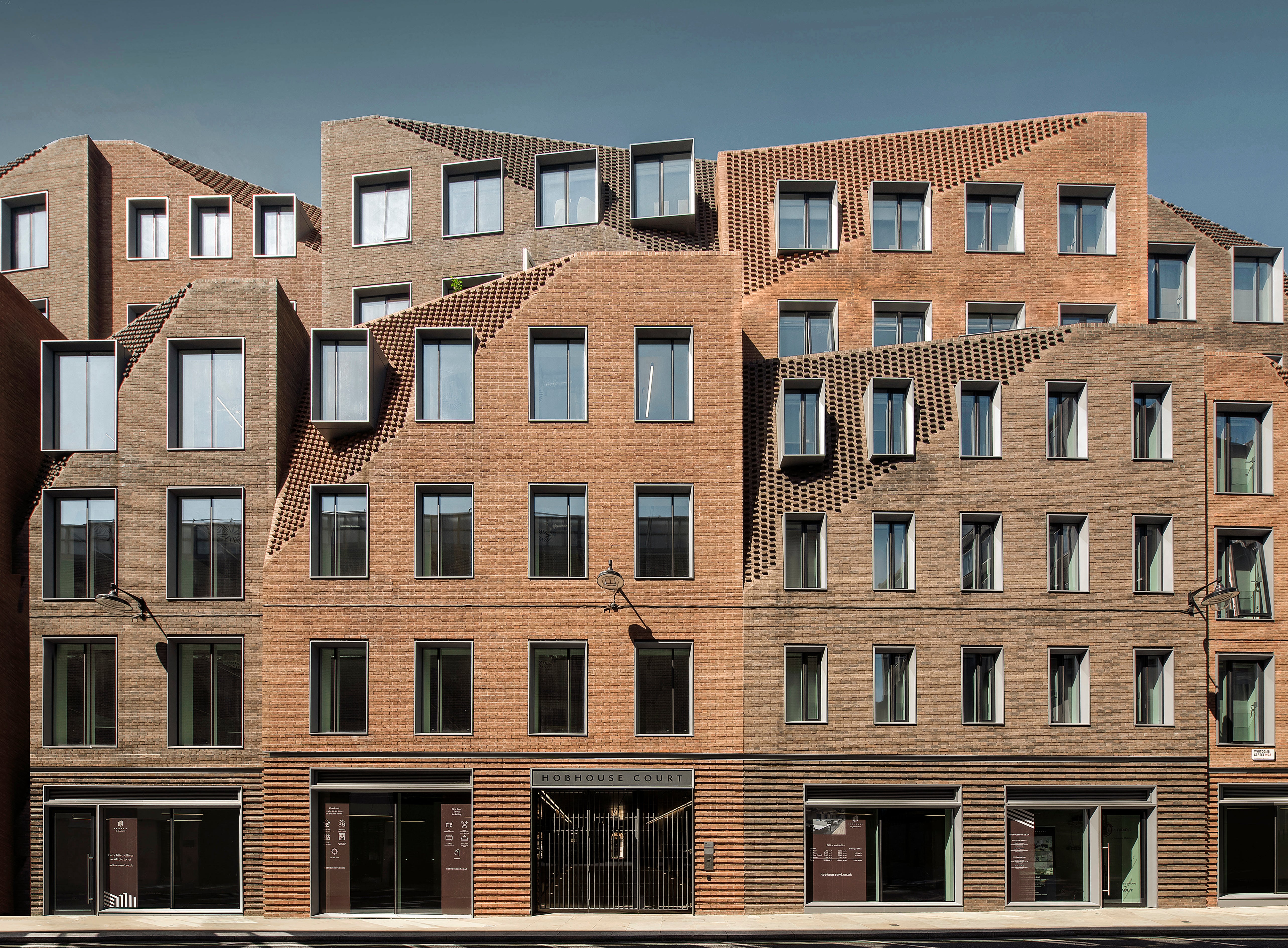
Another key feature is its innovation in climate-friendly manufacturing processes. HyBrick, a UK government-funded research project undertaken by Michelmersh in 2022, revealed for the first time on an industrial site the remarkable carbon-saving qualities of hydrogen-fuelled brick firing.
Over the three firing trials, it recorded an 80 to 84 per cent reduction in gas carbon emissions compared to natural gas. It was a world first: never before had a firing process been powered by green hydrogen alone on a brick manufacturing site.
For ceramics to significantly decarbonise, more government support is needed
HyBrick is part of a long-term ambition and commitment by the company to reduce emissions. It has already achieved a 20.1 per cent reduction in its carbon emission intensity since 2016, via several transformations to its everyday operations: investing in renewables and rainwater harvesting, for instance, and reducing use of single-use plastics – in fact, it was the first UK brick company to pledge to eliminate non-essential single-use plastics and is now currently trialling organic alternatives.
It is also the first brick manufacturer in the UK to introduce building information modelling (BIM) files. This gives all stakeholders in a building project, including the architect, contractor, facilities manager or owner, the key information on the physical three-dimensional and technical data characteristics of a facility and its products. This reduces the potential for waste in construction and improves resource efficiency.
Michelmersh has also launched sustainablebrick.com, which aims to showcase the many benefits of clay brick to specifiers, construction professionals, homeowners and housebuilders. This platform ensures architectural professionals are alert to the evolution and investment the industry is making towards innovative sustainability-related improvements, while showcasing the sustainable benefits of clay brick.
It also hopes to educate and inform SMEs among its peers within the construction industry of the many carbon calculation resources available to aid the sector in collectively and collaboratively hitting its Net Zero targets. Through the products and initiatives showcased throughout the website, it aims to inspire and revolutionise the way sustainable construction practices can be adopted for future generations.
Yet while HyBrick received vital support from the UK government, there is still much more to be done. Around 17,500 people work in the ceramics industry in the UK, producing materials that play a critical role in sustaining our way of life.
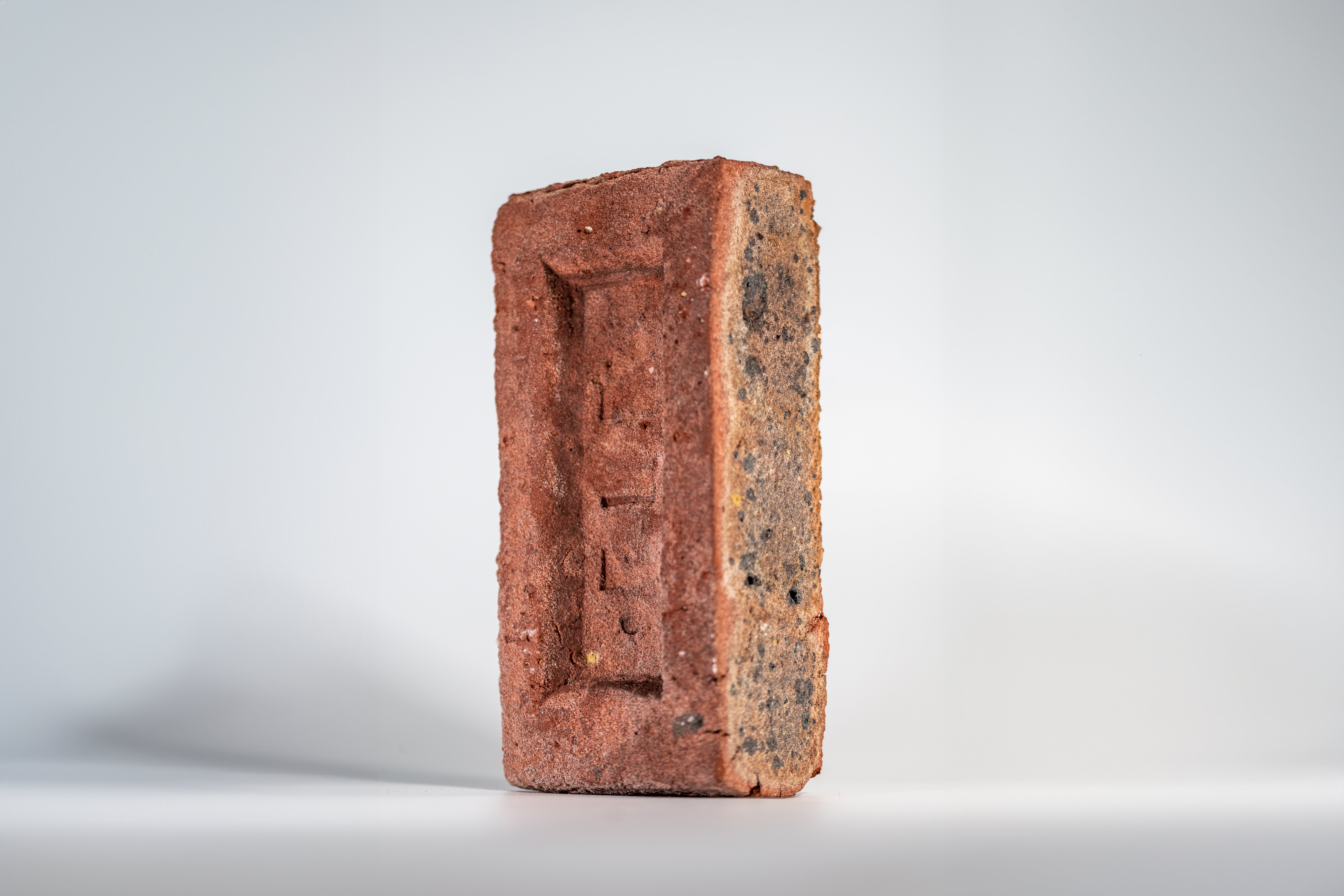
“Ceramics fulfil many essential, often surprising roles across the economy,” continues Sarah Le Gresley. “Ceramics manufacturers have continually invested in upgrading processes and technologies – over £750 million over the past 10 years alone. But 75 per cent of companies in the sector are small to medium-sized businesses who may struggle to afford to rebuild or retrofit sites with new, emerging technologies or fuels expected over the coming decades.
“Further decarbonisation will be challenging and complex, with various transition needs which will require collaboration and support from government and other parties.
“Ceramics UK – the national trade association – has just published an updated decarbonisation roadmap which sets out future industry ambitions and it’s crucial that we continue the conversation around how these can be delivered to ensure the ceramics industry is retained in the UK, rather than importing potentially higher-carbon goods from countries with lesser climate aspirations or obligations on producers.”
Michelmersh has provided an exemplary route towards decarbonisation, demonstrating how investment and commitment, from above and below, can drive innovation and move the industry towards the country’s Net Zero targets.
Click here to learn more from Britain’s Brick Specialists.
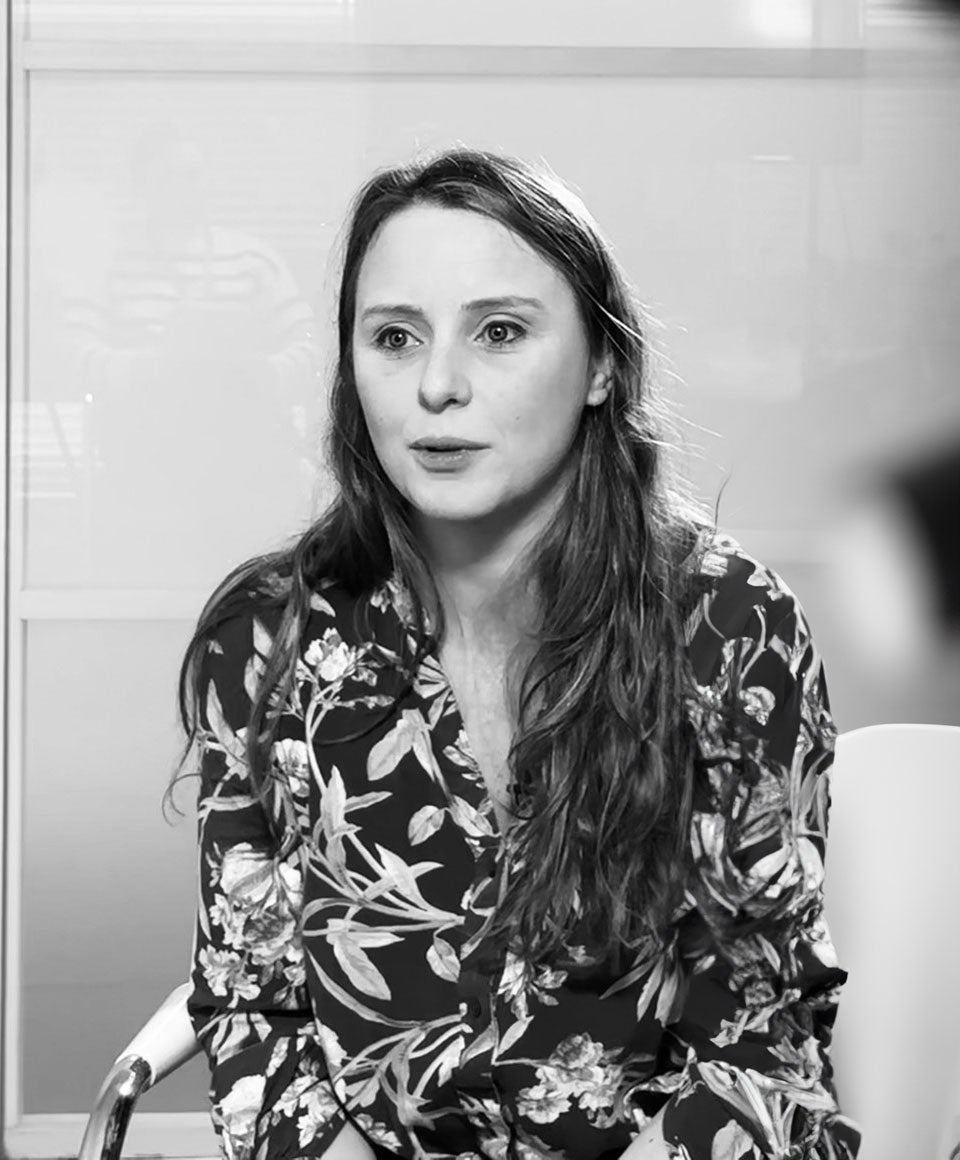