Squeaky clean Mclaren gearing up for growth
Tom Bawden visits the car manufacturer's spotless £50m plant, and finds it hopes to be a winner on the roads as well as F1 tracks
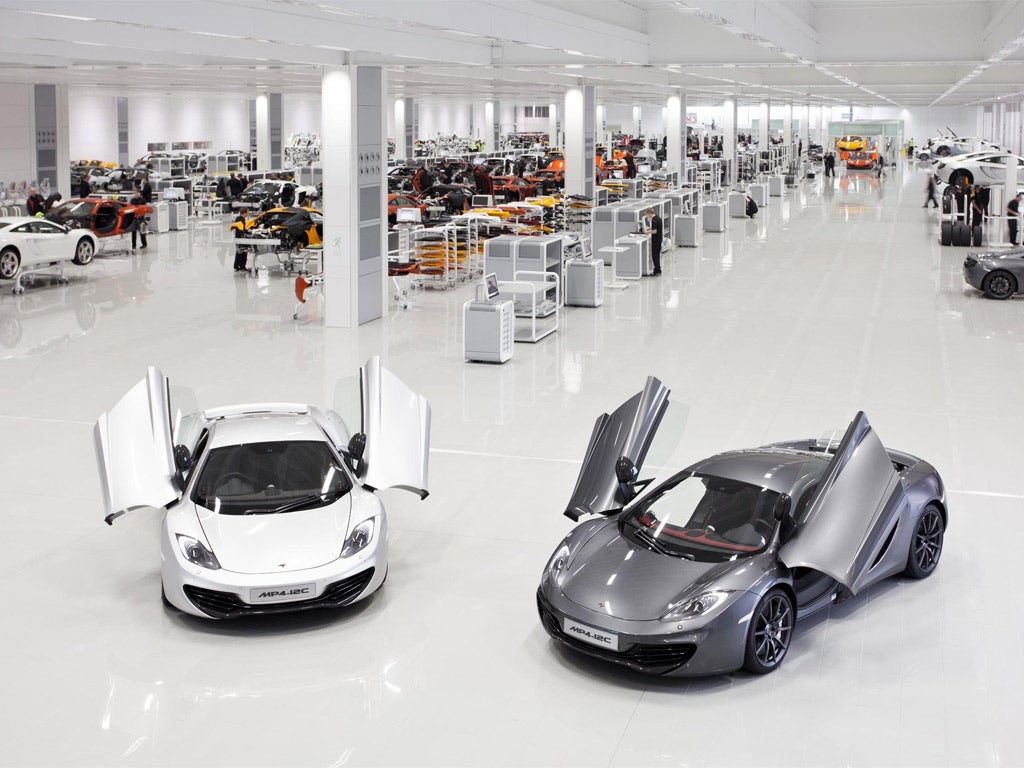
Your support helps us to tell the story
From reproductive rights to climate change to Big Tech, The Independent is on the ground when the story is developing. Whether it's investigating the financials of Elon Musk's pro-Trump PAC or producing our latest documentary, 'The A Word', which shines a light on the American women fighting for reproductive rights, we know how important it is to parse out the facts from the messaging.
At such a critical moment in US history, we need reporters on the ground. Your donation allows us to keep sending journalists to speak to both sides of the story.
The Independent is trusted by Americans across the entire political spectrum. And unlike many other quality news outlets, we choose not to lock Americans out of our reporting and analysis with paywalls. We believe quality journalism should be available to everyone, paid for by those who can afford it.
Your support makes all the difference.Arriving at McLaren's new, state-of-the-art "supercar" factory feels more like visiting a fabulously equipped hospital than a manufacturing plant. Sitting next to the racing car group's headquarters on the edge of Woking, the £50m Sir Norman Foster-designed production facility is almost entirely white, spotlessly clean, polished to a dazzling sheen and very, very quiet.
There are no blaring radios or oil patches, no unidentifiable screeching noises and no dubious wall calendars on the site, which was created to build McLaren's new £168,000 roadcar, the 12C, in the group's boldest-ever foray outside Formula One (F1) motor racing. The occasional car horn, the odd whirr of hi-tech equipment and the perpetually running polishing machine on what must be some of the world's cleanest floor tiles, are all that disturbs an almost eery silence.
This beautifully conceived, modern, highly functional space is undoubtedly a triumph of design and efficiency – except it almost feels a bit too perfect. In its pursuit of operational efficiency, the soul appears to have been left out, an omission which might, arguably, chip away at some of the productivity it was intended to promote.
Lee Boyce, McLaren Automotive's head of operations engineering, acknowledges that the facility "is very surgical in its approach … some people might find there's a degree of sterility to it". But Mr Boyce is clearly in love with the factory that isn't really like a factory. A car industry veteran, he has seen the plants of Lamborghini, Bentley, Aston Martin, Porsche and Rolls-Royce, but McLaren's new site is the least industrialised of them all, he says with evident pride.
The 2,000-odd components that make up the car are put together almost entirely by the hands of the factory's 200 assembly staff, with automation kept to an absolute minimum.
"There is an automotive feed system that takes paint from the vessel to the gun," Mr Boyce said, when pressed to explain which of the plant's activities are carried out by machines. "We wanted to emphasise the handbuilt idea to underline the fact that there is no significant industrialisation in the process. We didn't want to be like anybody else, so we came up with a concept that is very different from other factories."
The plant was formally opened by David Cameron in November, although it began making the MP4-12C mid-engine supercars – biggest competitor the Ferrari 458 – last spring.
McLaren has dipped its toe outside strict F1 racing before, selling 106 of its £1m F1 roadcars in the 1990s and about 2,000 SLR models during the following decade for an average of £300,000 through a now-defunct joint venture led by Mercedes.
The 12C marks McLaren's first attempt to extend its F1 racing brand by launching a road car in something approaching large volumes.
Antony Sheriff, the American managing director of McLaren Automotive, the division which makes the 12C, is understandably proud of the carbon-fibre-bodied vehicle and of the team that has designed and produced it.
Mr Sheriff, who claims to have been obsessed with cars since the age of two, likes to think McLaren is at the forefront of a new, hi-tech, face of British engineering, with the potential to lead the "march of the makers" that the country is relying on to dig it out of recession.
But there are two obstacles facing McLaren and, in turn, British manufacturing, says Mr Sheriff.
Sitting in his office at the group's space-age headquarters next to the 12C manufacturing plant, he is highly critical of Britain's treatment of engineering, an attitude he finds all the more puzzling because the country has produced so many top-flight engineers over the years.
"It's always a challenge to get very high-quality people. British engineers are brilliant but we just need an awful lot more," he told The Independent.
"One of the potential challenges in the UK is that there is not much of a culture of engineering being a noble profession like there is in Germany, the US and Asian countries like China, India and Korea," he added.
"If you look at the huge number of students coming out of pure technology and engineering schemes, it's nothing like as high as the US. I get the impression in the UK that classics, philosophy and finance are held in much higher regard, and if you can't do that, you go into engineering.
"There needs to be a push from government to encourage people into engineering to grow the economy. First and foremost, what drives industry is making things and that comes from technical progression."
The best way the Government can help, Mr Sheriff says, is by investing more in university technical schools.
McLaren Automotive employs 1,011 staff in total, mostly engineers and technicians. While it has been able to recruit the majority of those staff from the UK, 133 of them have been brought in from 26 other countries.
Italians are the most common, representing about a fifth of the overseas contingent. French are next, followed by Germans and then Americans.
Mr Sheriff's second beef with British manufacturing is the quality of the suppliers, which he says has declined along with the country's wider industrial base. McLaren is forced to rely on imports for 60 per cent of the parts for its 12C. Some 40 per cent of the components used in the vehicle are sourced from Europe, 20 per cent from even further afield, while just 40 per cent are produced domestically.
Mr Sheriff said "some parts are very difficult to get in the UK and it's a shame to always have to go to other countries" to get them, citing latches, lights, some body parts such as gearboxes and some electronics parts as being especially difficult to source.
"One of the things that has become very apparent is that a lot of local supply has become rather weak. We really do rely on strength and innovation from suppliers. We don't just need one or two hallmark companies."
But despite Mr Sheriff's misgivings about British manufacturing, it is inconceivable that the new McLaren plant wouldn't have been based in the UK and, more specifically, next to its F1 centre in Woking where it can draw on the skills built up over a period of decades.
McLaren has been based in Woking since 1981, when the group relocated from Windsor following its take over by executive chairman Ron Dennis, who was born, bred and based in the Surrey town.
Furthermore, despite a shortage of top-flight engineers, Britain is still the world leader in F1 racing and related engineering, with motorsport worth £5bn a year to the UK economy.
Rival F1-groups Renault and Williams are both based in the nearby county of Oxfordshire and Red Bull is in neighbouring Buckinghamshire, giving the south of England a considerable – if dwindling – base of suppliers as well as engineering expertise.
It's not that Mr Sheriff is unhappy with the Government's approach to manufacturing – it's just that he thinks it could do more, in particular to encourage investment. "I don't think there is anything the British Government is doing to make things difficult, quite the opposite," he said.
And he holds out hope that British car manufacturing might be turning a corner after years in the doldrums – with McLaren playing a small, but symbolically important role.
"The renaissance of JLR (Jaguar Land Rover) is helping to rebuild the car industry and this has improved the supplier base."
Although McLaren is likely to remain a niche player in the car market, it has high hopes for expansion.
The company's present capacity allows it to produce about 1,000 cars a year – there is a six-month waiting list – for which the US is by far the biggest customer snapping up about 40 per cent of cars, followed by the UK which accounts for about a quarter. The Middle East and Asia have each bought about 15 per cent, with the remaining five per cent sold to continental Europe.
Over the next three years, McLaren hopes to ramp up production of the 12C – and any new variants that might appear (the company is being tight-lipped on the details) – to around 4,500 vehicles a year.
In the short term, the growth of McLaren – and the wider car industry – will further increase competition for good, domestic suppliers and engineers. But in the longer term, the bigger the industry, the stronger the hub and the more talent it sucks in. Which can only be good news.
Revival: Car making makes a comeback
Britain's car manufacturing industry has rebounded strongly in the past three years after being turbo-charged by foreign-owned auto giants, such as the big three Japanese producers Toyota, Nissan and Honda.
Car production jumped by 5.8 per cent to 1.34 million vehicles in 2011 and output is expected to grow strongly over the next few years after UK-based car makers collectively pledged to invest £5.6bn here in the past 18 months. This will create about 15,000 new jobs in car manufacturing, design, retail and related products and services and by 2016 could see UK production exceed the record 2.33 million vehicles set in 1972, according to the Society of Motor Manufacturers and Traders (SMMT).
The number of cars made in Britain rose 17.3 per cent in the first five months of this year, compared to the same period in 2011.
Britain's car-making renaissance is clearly great news for the economy, with the industry now employing 140,000 people in manufacturing and design.
However, while a return to 1972 levels of car manufacturing is good news for the staff employed and the exchequer which receives their income taxes, it would be an exaggeration to say it would put the UK back where it was in the early 70s.
Back then, most of the production was carried out by British-owned companies. These days, most production is foreign-owned, meaning profits – and, often, associated work such as design – go overseas.
Furthermore, improved technology means the average plant worker can make ten times as many cars today as in 1972.
Join our commenting forum
Join thought-provoking conversations, follow other Independent readers and see their replies
Comments