Worth the lack of weight
A new piece of thin sandwich panel technology makes cars lighter and more efficient
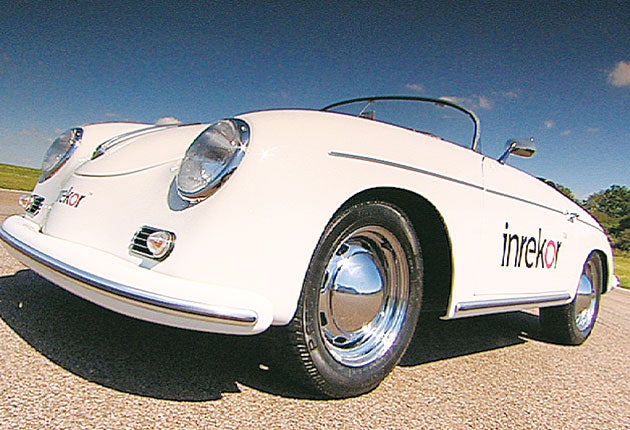
Your support helps us to tell the story
From reproductive rights to climate change to Big Tech, The Independent is on the ground when the story is developing. Whether it's investigating the financials of Elon Musk's pro-Trump PAC or producing our latest documentary, 'The A Word', which shines a light on the American women fighting for reproductive rights, we know how important it is to parse out the facts from the messaging.
At such a critical moment in US history, we need reporters on the ground. Your donation allows us to keep sending journalists to speak to both sides of the story.
The Independent is trusted by Americans across the entire political spectrum. And unlike many other quality news outlets, we choose not to lock Americans out of our reporting and analysis with paywalls. We believe quality journalism should be available to everyone, paid for by those who can afford it.
Your support makes all the difference.The motor industry has a weight problem. Car manufacturers have responded to environmental concerns and rising fuel prices by boosting engine efficiency as well as by developing new technologies such as hybrid drive-trains. Big improvements have also been made in aerodynamic efficiency. The new Seat Alhambra, for example, a big people-carrier, has a drag coefficient of 0.299, making it more slippery than the best cars of a few years ago.
But there has been little progress when it comes to the other big factor in fuel efficiency: weight. Today's sixth-generation Volkswagen Golf, to take a typical example, is as much as 50 per cent heavier than the 1974 original. It's all our fault, of course; we just aren't prepared to do without safety features such as air bags, or conveniences such as air conditioning and electric windows that were once regarded as luxuries.
With some of their latest models, manufacturers have been able to contain weight increases by, for example, using high-strength steels, while a few companies such as Jaguar have adopted lightweight aluminium body structures. There is also limited use of exotic expensive materials such as carbon fibre, but car makers are still looking for a big breakthrough that would allow them to take a lot of weight out of their vehicles on an affordable basis.
One promising approach comes from inrekor, a company that has developed a lightweight sandwich panel technology that may be capable of being integrated into today's big-selling cars, as well as being suitable for economical low- to medium-volume production of specialised models such as electric vehicles.
Sandwich construction, in which a single-sheet metal panel is replaced with two thinner sheets joined by a lightweight filling, is already widely used as a means of producing stiff, light structures in areas such as aviation. What is new about inrekor's approach is it believes it has found the right combination of materials and processes to allow it to be employed economically in mainstream car-making. As the company's sales director Freddy Page-Roberts says: "Sandwich panel for mass production: that's the innovation we've got here."
The filling in an inrekor panel is Arpro, an expanded polypropylene foam, and inrekor has also established links with the German adhesives manufacturer Henkel; effective bonding is crucial to the performance of sandwich structures. In future, it should be possible to make inrekor sandwich panels with the sort of complex curved shapes that make up cars' exterior bodywork, but at present the focus is on "2D to 3D", or building up 3D structures from a collection of flat panels.
One notable application of the process, which may not be typical of the way it will be used in future but certainly shows off its strengths, is a chassis designed to be integrated into the Chesil Speedster, a replica of the Fifties Porsche 356 Speedster produced by the Dorset-based Chesil Motor Company. The Chesil version requires a VW Beetle donor chassis; these were once plentiful, but the supply is now drying up. The inrekor version weighs 37kg instead of 122kg, and it is estimated that sandwich construction could be used to reduce the weight of a mainstream production car by about 300kg, enough to produce a saving of about 30g/km in CO2 emissions.
Central to the savings is "mass decompounding". It works like this. A car built according inrekor's architecture is lighter than a conventional vehicle of the same size, but that is just the start. Weight savings snowball because a lighter car can safely get away with lighter brake and suspension components, for example, which may allow another round of weight reductions and so on, so the overall weight loss may be much greater than that accounted for by the initial use of inrekor alone.
And the inrekor technology has other advantages as well. The company's technical director, Stewart Morley, says that inrekor panels have excellent noise and vibration characteristics, and their crash performance is very good for their weight; they can easily be "tuned" to optimise their behaviour in an accident. Production requires only low levels of capital expenditure, while the aluminium skin and the Arpro which make up the sandwich panel are claimed to be 100 per cent recyclable.
Inrekor is working with one major car maker and is in discussions with many more. It is probably too early to say whether the technology will break into the automotive mainstream, but we will certainly be hearing more about the role of weight loss and mass decompounding in helping car makers to meet their environmental and performance goals.
Join our commenting forum
Join thought-provoking conversations, follow other Independent readers and see their replies
Comments