Meet the friends who turned their unusual knife-forging hobby into a sought-after artisan business
The Belnheim Forge is part of the latest wave of DIY, artisan culture
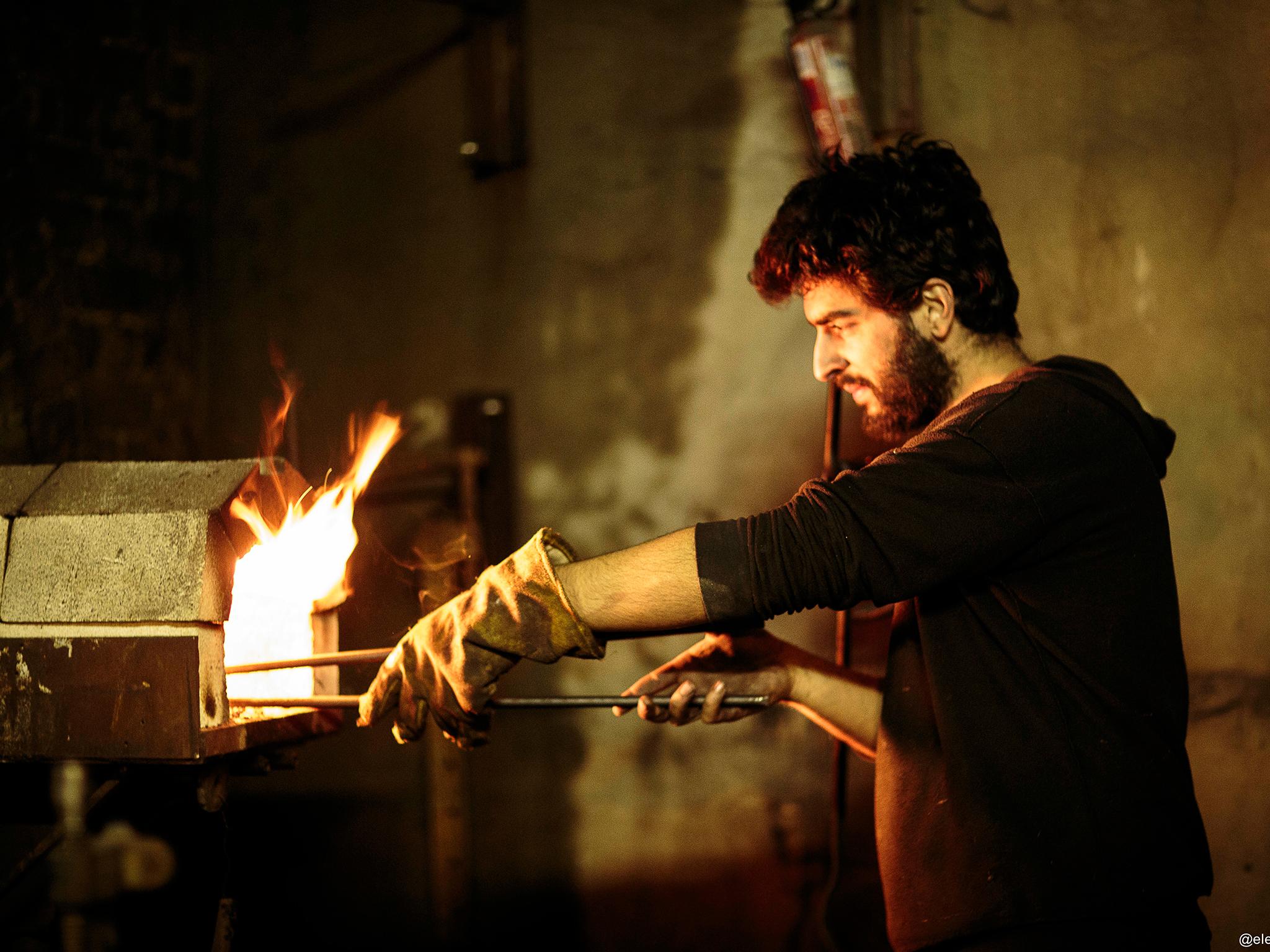
Your support helps us to tell the story
From reproductive rights to climate change to Big Tech, The Independent is on the ground when the story is developing. Whether it's investigating the financials of Elon Musk's pro-Trump PAC or producing our latest documentary, 'The A Word', which shines a light on the American women fighting for reproductive rights, we know how important it is to parse out the facts from the messaging.
At such a critical moment in US history, we need reporters on the ground. Your donation allows us to keep sending journalists to speak to both sides of the story.
The Independent is trusted by Americans across the entire political spectrum. And unlike many other quality news outlets, we choose not to lock Americans out of our reporting and analysis with paywalls. We believe quality journalism should be available to everyone, paid for by those who can afford it.
Your support makes all the difference.Blenheim Forge is an example of what happens when friends take an arguably ill-advised idea and run with it.
Knife-making started out as a hobby for Jon Warshawsky, 32, and his friends James Ross-Harris, 27, and Richard Warner, 29, as a way to explore whether scavenged materials and a few tools could be put to use.
A decade ago, setting up a forge in South East London would have sounded daft. But their hobby was perfectly timed to coincide with a resurgence in DIY culture – from craft beers to home baking and knitting – and the trio were able to set up a workshop 10-minutes walk from their shared home in Peckham, south east London, in 2013 - a year after they started dabbling in their back garden.
Their wares - priced between £140 to £280 - are now in demand with both professional chefs and dedicated home cooks, and they have taken on workers to cope with the number of orders they receive.
“I think people like to have a really clear idea of something’s provenance, knowing it has been made by someone who really cares about their craft rather than churned out of some factory is very appealing to a lot of people,” Warshawsky tells The Independent. “Quality is also a big factor- a stamped out, mass produced blade can never compete with a good hand-forged knife.”
But, unsurprisingly, the making a knife isn’t as easy is it sounds.
“There's two parts of the process that have caused us the most trouble: the forge weld, and the hardening. Forge welding is the process of fusing together different metals to create the layered structure that is typical to our blades. This has to be done in fairly precise conditions in order to be successful. The preparation of the steel, the temperature and amount of oxygen in the forge, and the correct working of the billet, all have tight margins of error."
This is, frustratingly, a problem only identified when the blade is finished.
“We have managed to bring our success rate for this stage up from around 1 successful attempt in every 10 to maybe eight out of 10 on a good day," says Warshawsky.
“The hardening is part of the heat treating process where the desired molecular structure of the blade is achieved. It's a violent process where the blade is heated up to around 800 degrees and then cooled down very fast by quenching in oil or water. This can cause warping of the blades, cracks along the edge, and blades snapped in half.”
Undeterred, their techniques are constantly changing and evolving while staying true to their ethos.
“In the recent couple of years we have definitely seen a lot more people popping up who are making really amazing handcrafted goods," says Warshawsky. "It is definitely not a dying art.”
Join our commenting forum
Join thought-provoking conversations, follow other Independent readers and see their replies
Comments