Get into the groove: why the demand for vinyl LPs is outstripping supply
Many believe the vinyl resurgence is nothing but a bubble waiting to burst, but Steve Boggan believes otherwise. There’s nothing else to be invented, so those tactile long-playing discs are here to stay
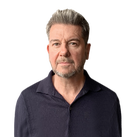
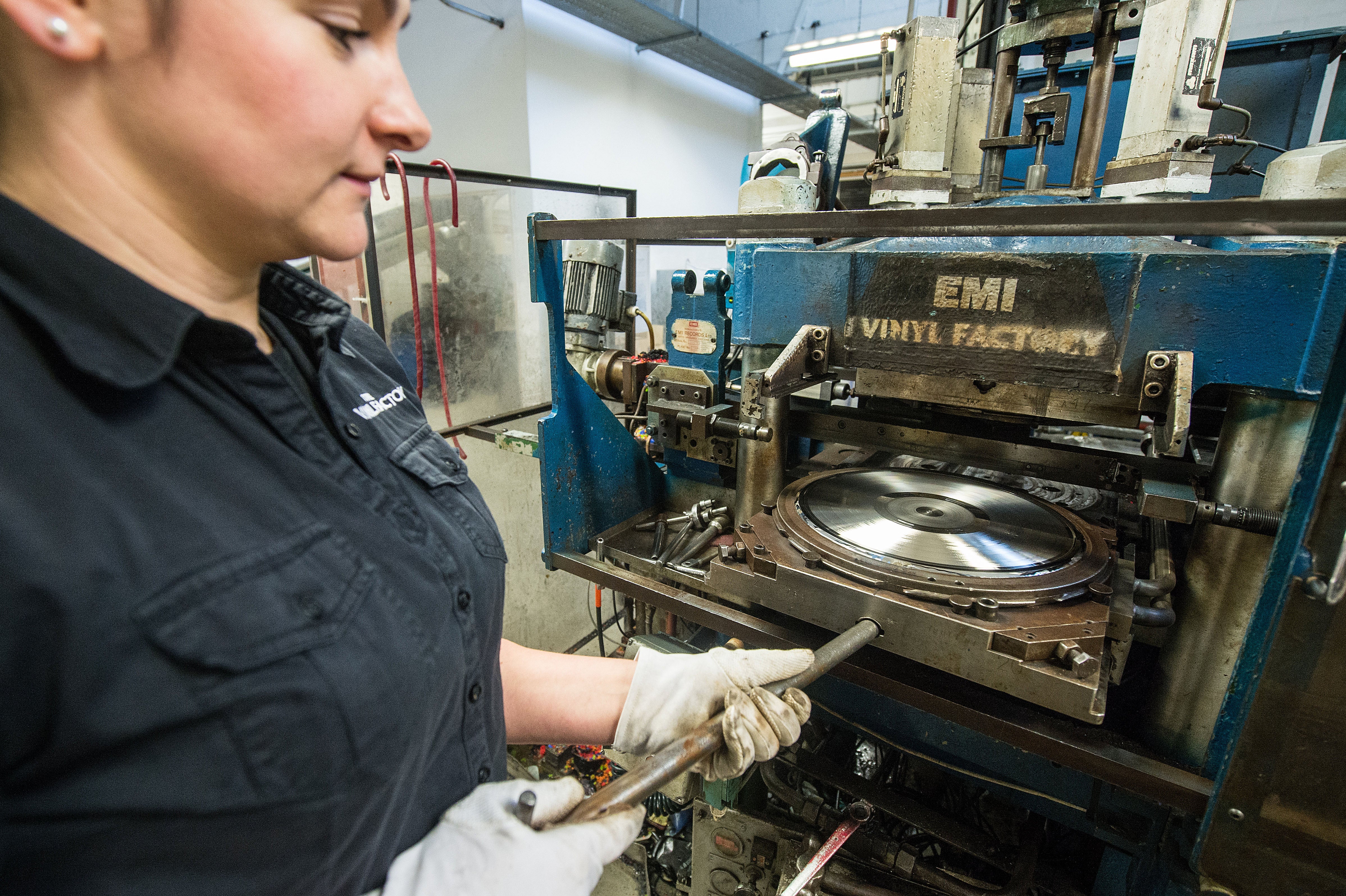
In 1903, Charles H Duell, commissioner of the US Patent and Trademark Office, supposedly resigned from his post after arguing that “everything that can be invented has been invented”. Duell didn’t actually say that – in fact historians have established that the quote came from a cartoon in Punch magazine – but I’m appropriating it anyway in support of my theory that vinyl records have a rosy future. They’re not going away. Their unexpected renaissance is not a bubble that will burst any time soon.
“Cassette tapes died out once you could record Top of the Pops on video,” I say to veteran vinyl manufacturer Adam Teskey. “People started turning their backs on CDs once iTunes came along. And now you can stream as much music as you want, all the time, through headphones which don’t have wires that fall into the gravy on your chips… and yet people still want vinyl. There’s nothing left to be invented as a music delivery system, so LPs are here to stay.”
Of course, this sounds as mad as Duell’s misattributed quote. I’m offering it to Teskey, the 54-year-old manufacturing director of the Vinyl Factory, Britain’s largest producer of vinyl records, in Hayes, west London, but he doesn’t look entirely convinced by my logic. “You might be on to something there,” he says, kindly.
Teskey, who is not only kind but also very cool, has been in the business since 1987 and that means he’s seen vinyl sales badly hit not once, but twice. First, with the arrival of CDs in the 1980s and then when the financial crash of 2007-08 hit the music industry hard. This means that while he’s optimistic about the future of vinyl, he’s also cautious, a caution I don’t share because of a toxic mix of bias, nostalgia and rose-tinted spectacles.
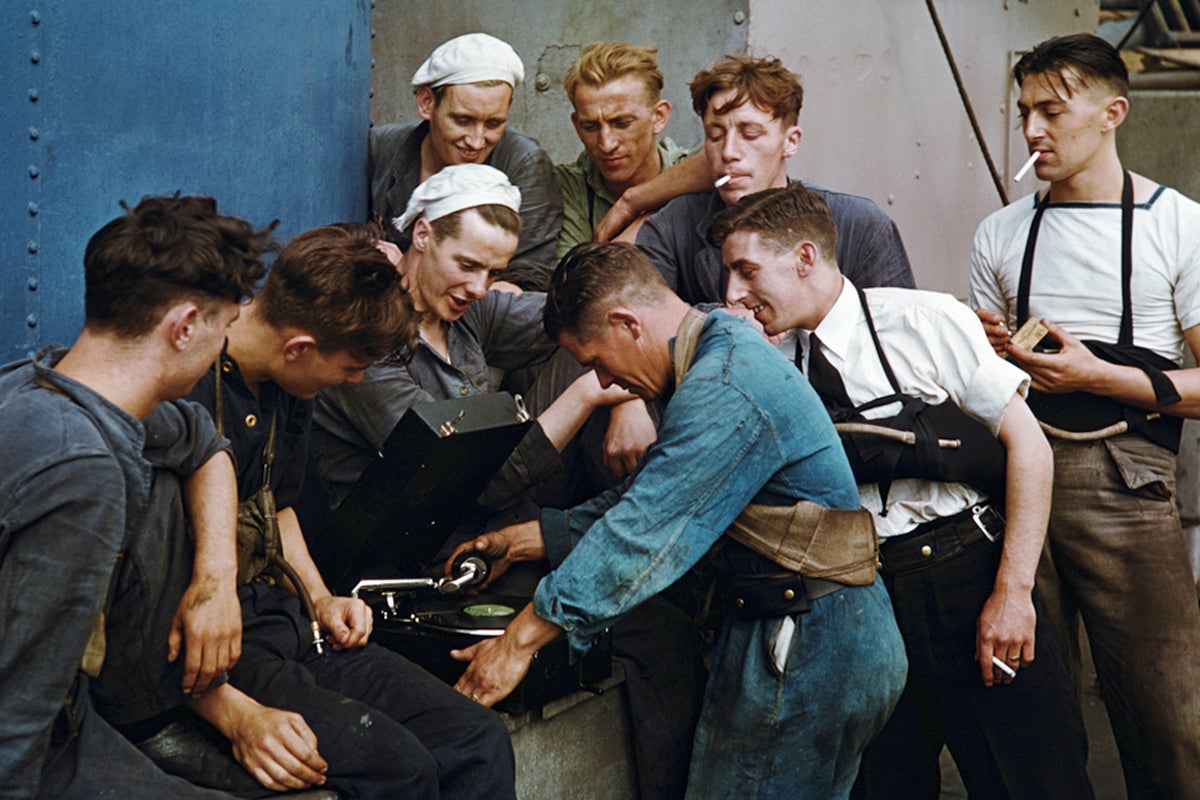
Last year, UK spending on LPs overtook CDs for the first time since 1987 (when Rick Astley was topping the charts). That brought in £86.5m from the sale of 4.8 million records – up by 30 per cent since 2019. And during the first quarter of 2021 – when lockdown saw audiophiles spending money on upgrading their collections from CD to vinyl – sales were up a further 16.1 per cent year-on-year.
So, why the caution? Well, because in spite of the booming sales, the optimism and the restoration of vinyl as the coolest way to enjoy music, a perfect storm – generated by Covid-19 and a shortage of skills, machinery, raw materials and investment – has left manufacturers struggling to keep pace with demand. And nobody is sure what that could mean for the long-term future of vinyl.
The Vinyl Factory is among producers in the UK, Germany, the US and the Czech Republic – all the main centres of vinyl manufacture – which have had to temporarily close their doors to new customers or introduce much longer lead times. Instead of a couple of months, record labels – particularly small independents – are now looking at nine months, and in some cases more than 12, before they can get their artists’ music pressed and ready to go.
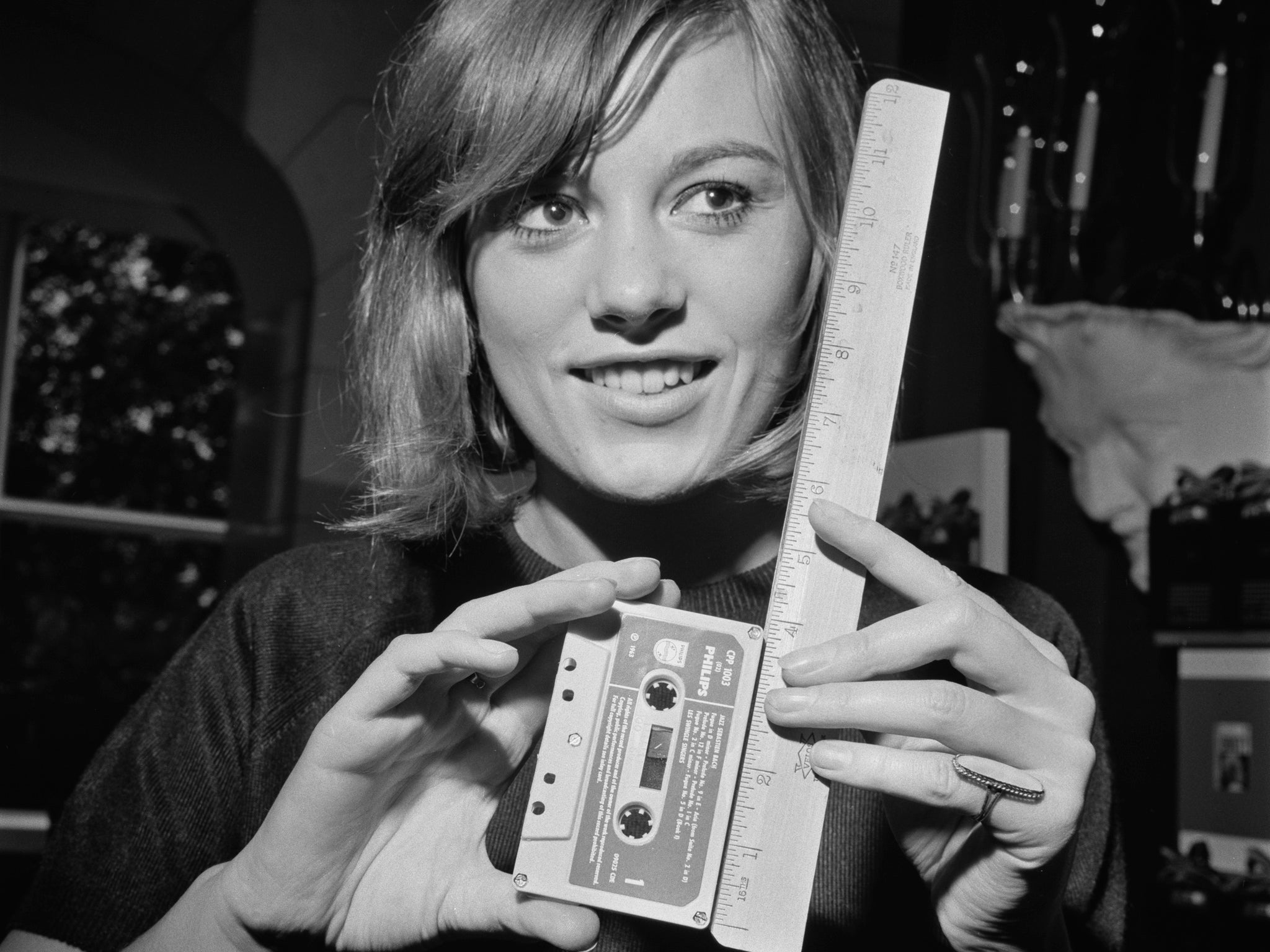
It would be easy to say that the sector is a victim of its own success, but, as we shall see, it’s more complicated than that. First, though, Teskey – who is such a good sport that he doesn’t even laugh when I tell him my first LP was Endless Flight by Leo Sayer – takes me on a tour of the factory to see how records are made. I am like a puppy with two tails (and, in my own defence, the second album I bought was Hunky Dory by David Bowie).
In spite of their standing as low-tech, there is nothing easy about making vinyl records. First, a master disc comprising an aluminium core coated in nitrocellulose lacquer is produced by recording studio engineers using a lathe. This is done to microscopically high standards; and, yes, the end result, representing the highs and lows of the recorded source material, is one continuous groove, usually defined by a sapphire-tipped cutter.
At the factory, the master disc, called the lacquer, is used to create a “stamper”, the relief that will be used to press records, in a process that involves electroplating with tin chloride and liquid silver.
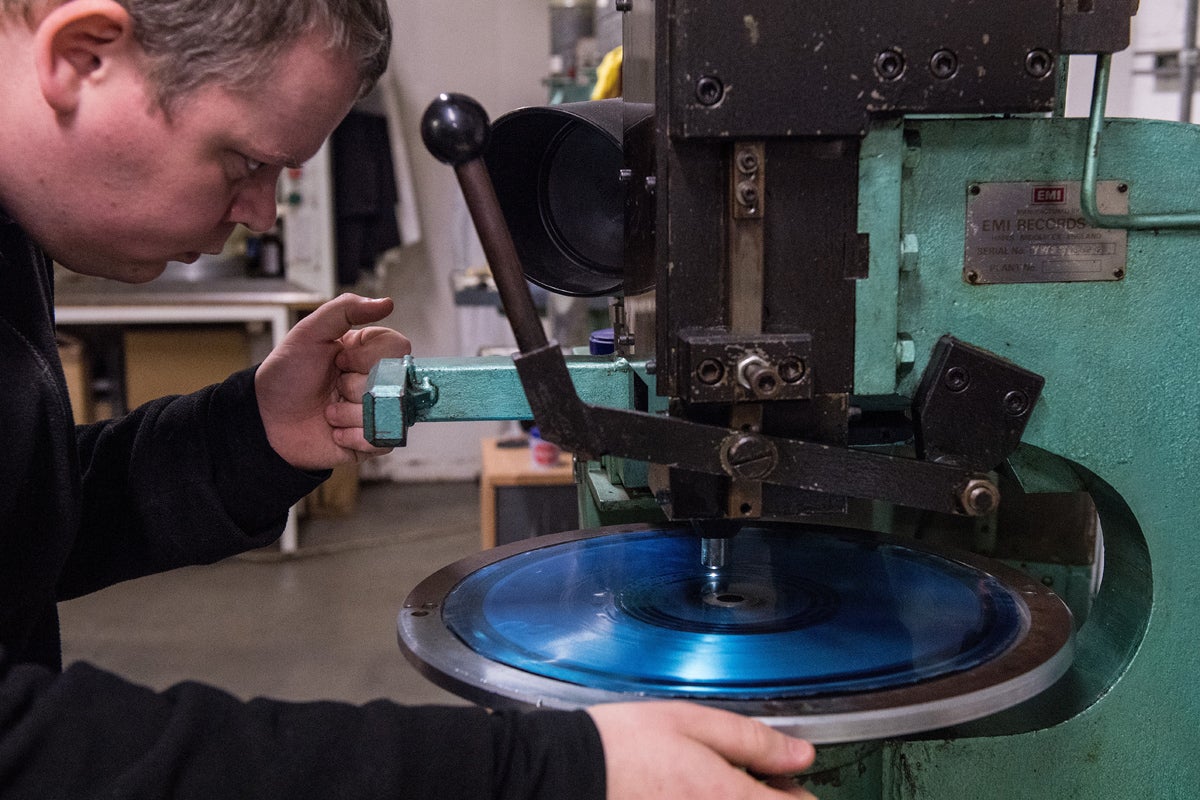
Before attaching the stampers to heavy circular steel moulds ready for pressing, they must undergo strict quality control. If there are any flaws, they are thrown away and the process begun again. At the Vinyl Factory, they still have a piece of quality assurance kit that was first used to check the standard of The Beatles’ Sgt Pepper’s Lonely Hearts Club Band. It’s a turntable on a wooden desk and it remains as elegant today as it was in the Sixties.
Teskey moves me across the Vinyl Factory floor to witness production on six EMI 1400 automated presses. The 1400 was also made in the Sixties – at the EMI factory just over the road in Hayes where, between them, EMI and HMV employed around 20,000 people (there are 33 employees here today). The machines were shipped by the dozen to factories all over the world, but these are the only ones left. They brought to the masses music by The Beatles, Elvis, The Clash, Pink Floyd, the Sex Pistols, Radiohead, Lou Reed, Björk and a host of others. They are clunky, noisy and quite beautiful.
On these presses, “pucks” made from polyvinyl chloride (PVC), and already bearing labels top and bottom, are flattened and pressed under 90 tons of pressure at 160C. I watch in awe as a record is pressed every 29 seconds. Today, it is a re-pressing of Uncle Acid and the Deadbeats’ 2011 album Blood Lust released by Rise Above records and pressed on purple sparkle vinyl.
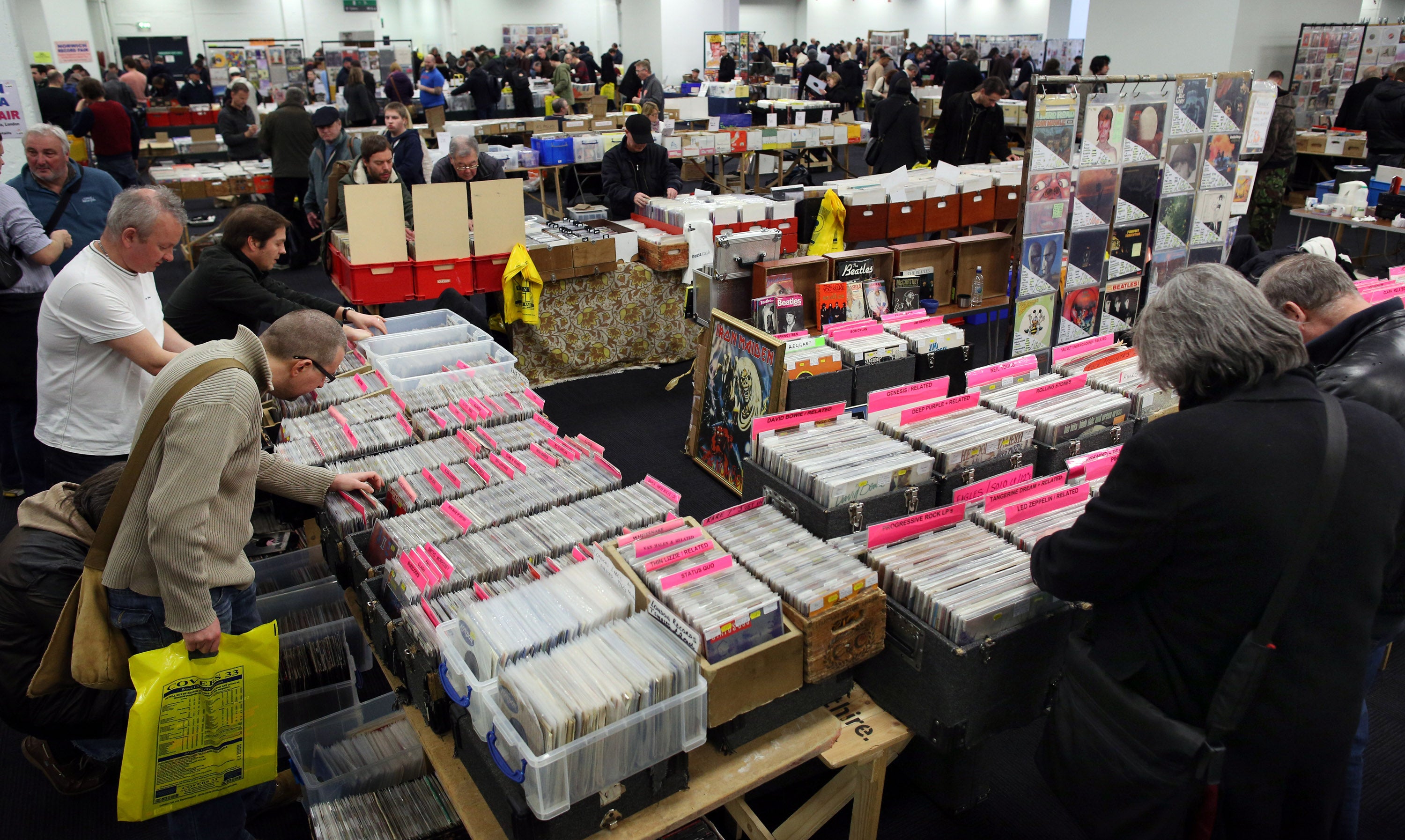
The fact that Rise Above is a small independent label is significant and demonstrative of the fact that in the world of LPs, the Vinyl Factory is one of the good guys. This is because a shortage of capacity has resulted in the feeling that other producers are accepting big orders for classic legacy recordings – such as, famously during the pandemic, Rumours by Fleetwood Mac, which kept selling out – ahead of small runs by independents.
The other big producers – ranging from Optimal and Pallas in Germany, GZ in the Czech Republic and Takt in Poland – deny this but independent labels feel they are being unfairly treated, not least because it was them, and not the big record labels, who provided the demand that kept manufacturers alive during the 1990s.
“I have no doubt that a 5,000 pressing of Rumours by Fleetwood Mac will find itself on a press much quicker than the 10 times 500 pressings I have in the pipeline,” said Danny Ryan, managing director of music distribution company Kudos Records in a recent interview with Investment Monitor. “I think this is why major label pressings are getting prioritised. They press in greater volume.”
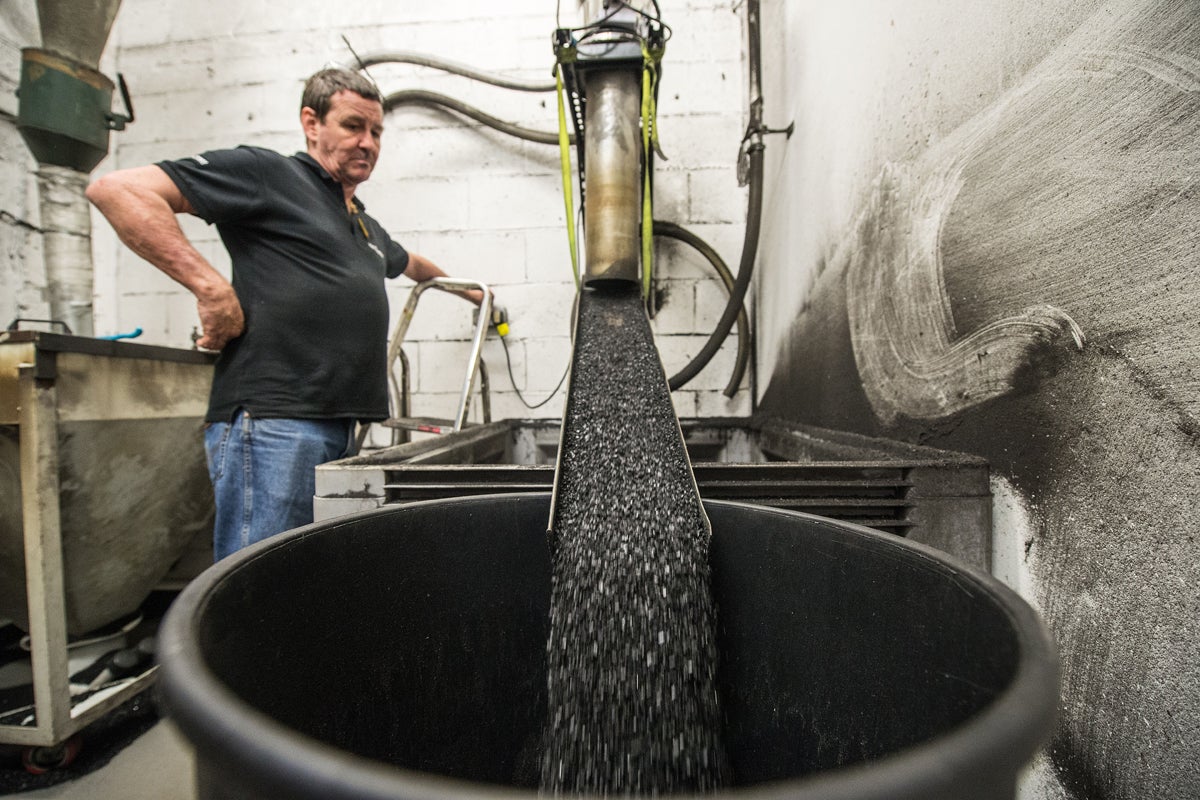
A senior executive at one plant, who did not want to be named, told me: “We’ve had production shut down after staff became ill with Covid, while supplies of PVC have been affected by the pandemic in India, where much of it is made. The cost of PVC pellets, which we use in the production of LPs, has recently gone up by 30 per cent.
“Add to that the fact that during lockdown, sales increased dramatically because people had more time and money to spend on listening to vinyl LPs, and that lots of musicians have made the landmark album they’ve always been dreaming about – and want it pressed – and you have the perfect storm. So, if a big label puts in an order for 10,000 units, can you really blame the manufacturer for taking that ahead of one for 300 from an independent label?”
Teskey won’t be drawn on the business practices of other manufacturers. “What I will say is that we don’t do that here: it’s strictly first-come, first-served among our regular clients,” he says. “But because of the growth in demand, we have had to temporarily stop taking orders from new ones.”
In January 2021, Teskey was processing orders for 370,000 records. That figure is now 680,000 and he’s working 110-hour weeks.
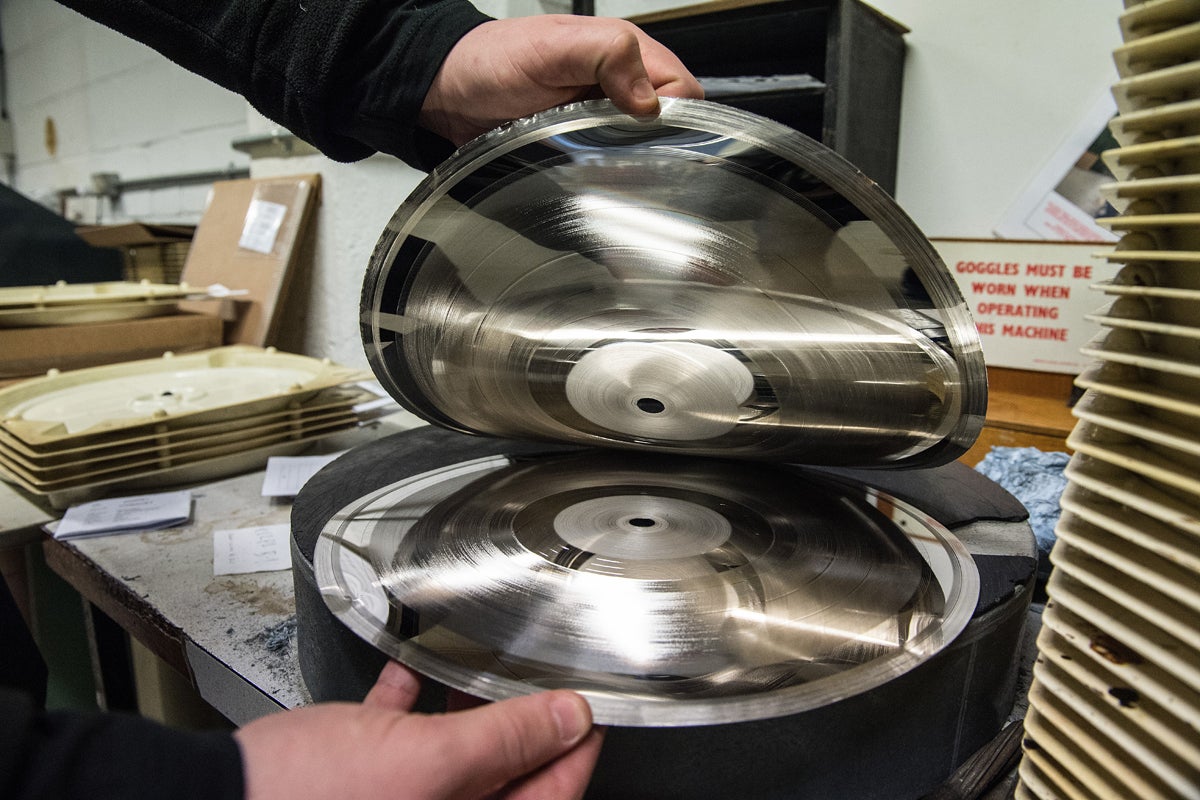
So, investors and record companies must be rushing to build new vinyl factories to cash in on all this new demand? Well, a little, but not enough. In an in-depth examination of the vinyl shortage published earlier this year, John Earls of the music website superdeluxeedition.com asked the British Phonographic Industry (BPI), the voice of the record companies, whether any new plants were in the pipeline.
The BPI told Earls: “We’re not aware of one being planned. That doesn’t mean it’s not being considered somewhere in the industry, we’re just not able to say one way or the other. It’s hard to say how productivity at the existing plants could be improved any further, as labels, distributors and so on have been working hard to achieve this already.”
Ever since the vinyl revival began more than 10 years ago, people have been predicting it would run out of steam but, as of this week, sales in the UK are 30 per cent higher than they were last year
Earls added that pressing plants, their brokers and record stores would love to see it happen but one major label executive told him: “I don’t see a new plant happening. Factories are incredibly expensive to build. It’s a massive investment.”
And, of course, with vinyl’s rollercoaster history, few investors are ready to lay out the millions needed to meet today’s growth in demand because they fear it might not be there tomorrow.
Keith Negus, professor of musicology at Goldsmiths, University of London, says nobody really knows. “As I frequently say to my students (as a way of provoking a discussion): if you had a million pounds to invest and you wanted a return on that investment, would you invest in musicians or in the manufacture of toilet rolls or toothpaste? Would you invest in a vinyl production plant and training for vinyl producers, or in Spotify and the designers of algorithms?”
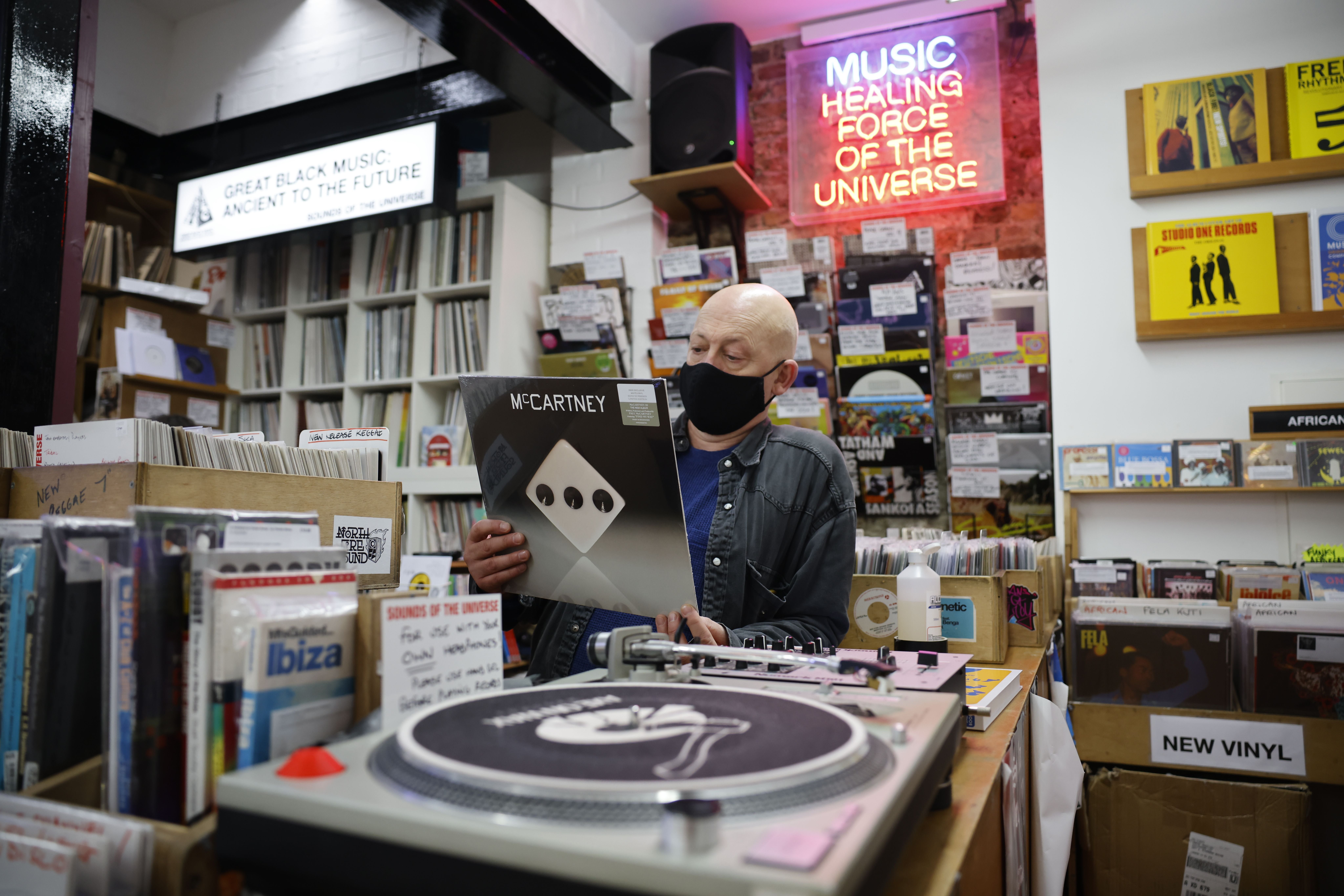
So, are we witnessing a bubble that will burst? He responds: “If I knew the answer to that I’d be in the music business and making lots of money and not working in a college.”
Whether or not vinyl sales will continue to grow is not something that is overly exercising the record industry. In the US, for example, while the medium is becoming more popular, it accounts for only a fraction of overall sales. Revenue from streaming dwarfs it – $10.1bn compared with just $619m.
However, it’s a figure that, as in Europe, is growing, and so executives can’t ignore it. Ben Katovsky, London-based chief operating officer of BMG, the world’s largest music publisher, tells me: “Vinyl isn’t growing in spite of the switch to streaming; it’s growing because of it. The more intangible music becomes, the more we’re seeing people want to buy the physical artefact. Barring wax cylinders – and no one’s predicting a return for them – vinyl LPs are the ultimate analogue format.
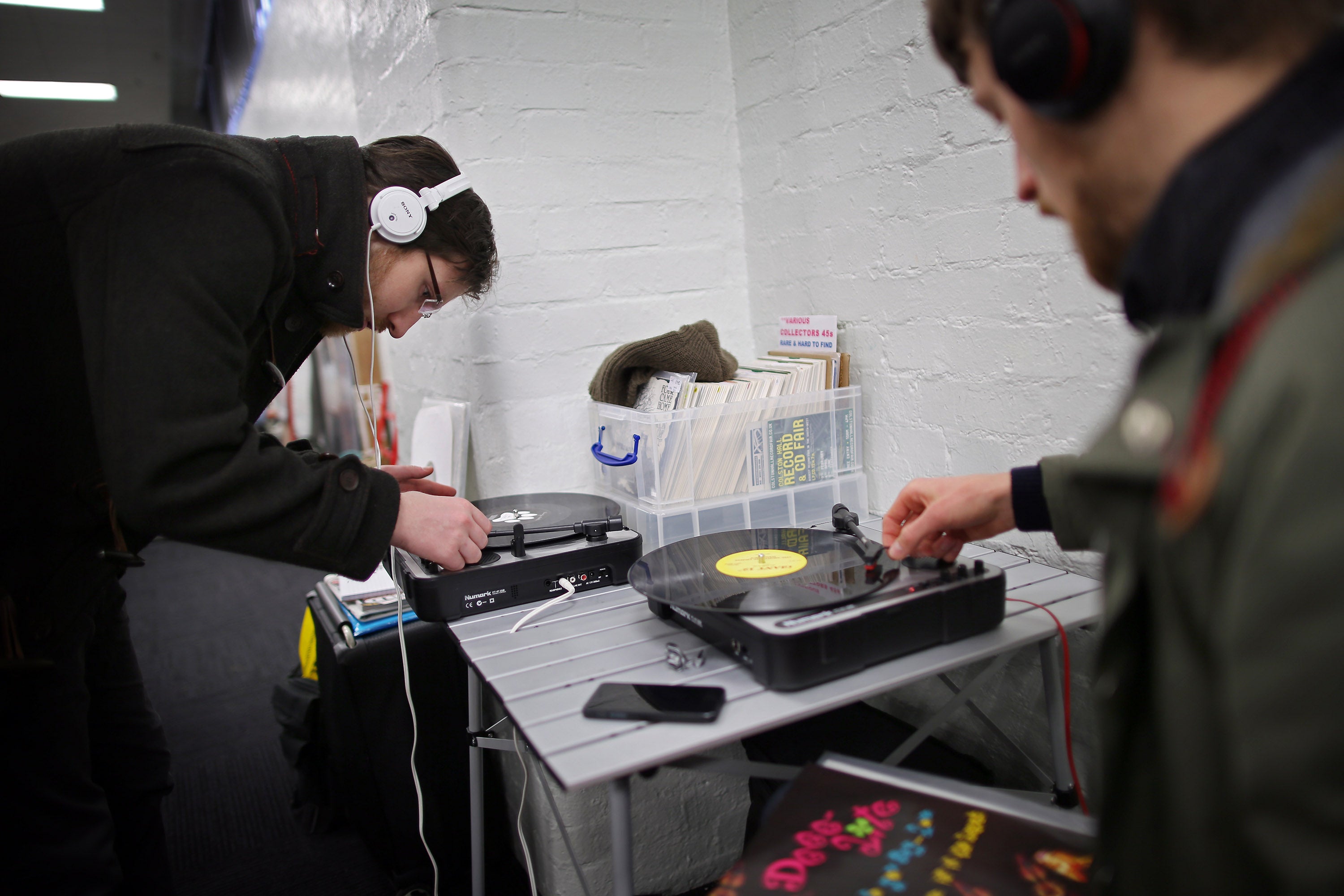
“Ever since the vinyl revival began more than 10 years ago, people have been predicting it would run out of steam, but as of this week, sales in the UK are 30 per cent higher than they were last year. This trend has still got some way to run.”
Perhaps the last word should go to Matt Colton, three-times winner of the Music Producers Guild’s coveted Mastering Engineer of the Year award. Matt has mastered vinyl records for Thom Yorke, Coldplay, George Michael, Peter Gabriel, the Arctic Monkeys, Elbow, Hot Chip, James Blake, Muse and a host of others.
“We’re starting to see examples of albums being released with the vinyl version following two or three months later,” he says. “For some artists, it isn’t right to delay their release to coincide with the LP. They just can’t wait. Vinyl is incredibly successful at the minute and people are making money from it, but it isn’t going to provide the majority of sales. It is just a small proportion of total sales, so it isn’t sensible to hold back and wait for your LP to be pressed. Even though people can get access to the music digitally first, they are still waiting for the LP. Buying the vinyl format fulfils an innate human desire to own a tangible object.
“Vinyl records are beautiful and they don’t cost a fortune. They complement streaming, and I don’t think anyone saw that coming. Streaming is convenient and obviously portable but sometimes listening in this way can feel like a secondary activity. To a degree, the music is in the background.
“But when you pick up a vinyl LP and take it out of its sleeve, with the crackle of static and the smell of the plastic, you see the artwork and sit down to read the lyrics and sleeve notes, it becomes your primary focus, not least because you have to physically get up and turn it over in 20 minutes. It transports you, and there’s nothing quite like it.”