Forget the A-listers – Leicester factory workers have already won their Oscar
Midlands company has had several famous visitors, including Stanley Kubrick, during more than a century of lens making
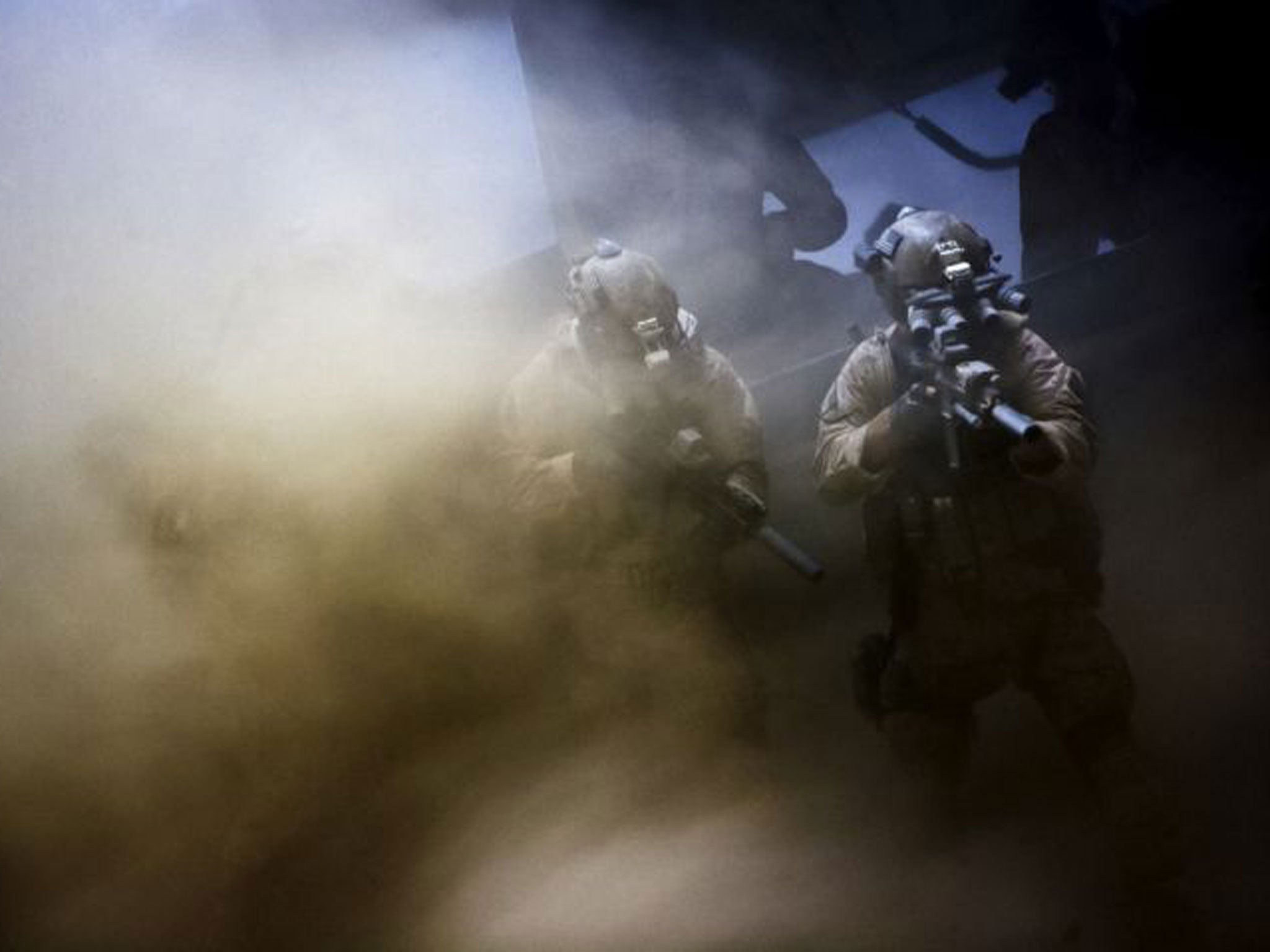
Your support helps us to tell the story
From reproductive rights to climate change to Big Tech, The Independent is on the ground when the story is developing. Whether it's investigating the financials of Elon Musk's pro-Trump PAC or producing our latest documentary, 'The A Word', which shines a light on the American women fighting for reproductive rights, we know how important it is to parse out the facts from the messaging.
At such a critical moment in US history, we need reporters on the ground. Your donation allows us to keep sending journalists to speak to both sides of the story.
The Independent is trusted by Americans across the entire political spectrum. And unlike many other quality news outlets, we choose not to lock Americans out of our reporting and analysis with paywalls. We believe quality journalism should be available to everyone, paid for by those who can afford it.
Your support makes all the difference.While Hollywood’s biggest stars face an anxious wait to see who will be honoured at the Academy Awards in a fortnight, a group of factory workers from Leicester can feel rather smug.
The 90-strong workforce at lens maker Cooke Optics already know that their handiwork will be bringing the coveted Oscar statuette back to the UK, to honour their contribution to “defining the look of motion pictures over the last century”.
Their employer is among nine recipients of honours at today’s Scientific and Technical Awards in Los Angeles, which are run by the Academy of Motion Picture Arts and Sciences to acknowledge behind-camera achievements. Cooke Optics is the only firm to secure an Academy Award of Merit, which comes with an Oscar statuette.
Managers Paul Prendergast and Keith Wykes, who started on the factory floor, will be among those welcoming the Oscar to their Leicester HQ. Mr Prendergast, who is 48 and started as a glass polishing apprentice, said: “What a fantastic achievement the Oscar is. We’re all so proud.”
Mr Wykes, 46, joined straight from school at the age of 15. During the early years he learnt how to polish, edge and grind the glass and is now the line manager for the miniS4 range of lenses. He described the company as “more of a Leicester secret than Richard III’s bones”.
Cooke has been around as long as the film industry and its lenses have shot everything from the Keystone Cops and Laurel and Hardy to this year’s best film contender Zero Dark Thirty. “To sit and watch a film where you’ve played a part in making those lenses… it’s a great feeling,” Mr Prendergast, now the glass production manager, said.
Cooke’s first photographic lens was created in 1894 and has been used on Sir Ernest Shackleton’s expedition to the South Pole, Royal Weddings and pretty much every Hollywood film in the 1920s including the first Oscar winner, Wings, in 1927.
“We’ve been there since the beginning, we’re older than Kodak,” Les Zellan, the owner of the company, said. “And it’s been in Leicester since then.”
Their lenses are still used by the biggest studios today on films from Martin Scorsese’s Hugo, which won best cinematography last year, to A Good Day to Die Hard. Even Downton Abbey has benefitted from the so-called “Cooke Look”. Mr Zellan said: “That’s our secret sauce. It is a very flattering look for skin tones. It really brings extra definition to two dimensional images.”
The Academy said: “These lenses have often been the lens of choice for creative cinematographers worldwide.” There have been a few high-profile visitors to the factory over the years, including Stanley Kubrick who picked up the lenses used to film A Clockwork Orange. Lord Attenborough opened Cooke’s new factory.
A set of lenses cost anything from $55,000 to over $200,000 at the high end. “The lenses take about a week to make from start to finish. We need to get the glass right, it needs to be of good cosmetic quality,” Mr Prendergast said, and added that while modern procedures and technology has moved on, “the physical fitting the glass to the metalwork hasn’t actually changed.” Some of the equipment still in use, is over a century old.
Join our commenting forum
Join thought-provoking conversations, follow other Independent readers and see their replies
Comments