Tweed recipes: Shear brilliance
Harris Tweed has been the backbone of beautiful suits for more than a century. As a new book celebrates the craftspeople behind it, Alice-Azania Jarvis charts the fabric's journey from sheep to Savile Row
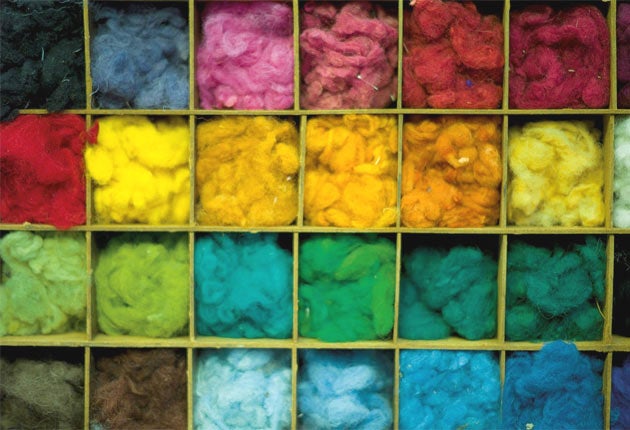
Your support helps us to tell the story
From reproductive rights to climate change to Big Tech, The Independent is on the ground when the story is developing. Whether it's investigating the financials of Elon Musk's pro-Trump PAC or producing our latest documentary, 'The A Word', which shines a light on the American women fighting for reproductive rights, we know how important it is to parse out the facts from the messaging.
At such a critical moment in US history, we need reporters on the ground. Your donation allows us to keep sending journalists to speak to both sides of the story.
The Independent is trusted by Americans across the entire political spectrum. And unlike many other quality news outlets, we choose not to lock Americans out of our reporting and analysis with paywalls. We believe quality journalism should be available to everyone, paid for by those who can afford it.
Your support makes all the difference.Derek Campbell shears the sheep. David McLeay dyes the wool. And Donald Murray weaves it. On the weather-beaten isle of Harris, just off the west coast of Scotland, these activities have made up the economy for generations. It's here that Harris Tweed (Clo Mhor in the original Gaelic "the big cloth") is made. The most famous of all the tweeds, it has been turned into suits since 1909, shortly after the new-fangled Trade Marks Act allowed nimble-fingered residents to put a stamp on their designs and ship them off to London.
Photographer and journalist Lara Platman left her home in Gloucestershire to spend a year with Campbell, McLeay, Murray et al. Her intimate portraits, laid out in Harris Tweed: From Land to Street, follow the fabric as it is created: from the birth of the Cheviot lambs, to their shearing, the washing and sorting of the fleece and the creation of the yarns, right up until the final moment – the gentleman's suit, proudly displayed, on a mannequin in a Savile Row tailor's window.
Throughout, personal stories punctuate the process. Katie Campbell has been weaving since 1967 – it's her wool pictured on the line above, overlooking the Little Minch sea. She weaves independently, inspired by the colours in the landscape around her, and then takes her tweeds to the Harris factory for approval. No patterns are written down; she does it all from memory.
Elsewhere, an unnamed shearer shows off his rare ability to shear by hand – a skill he shows off at competitions around the country – while George Graham, Stamper of the Orb, works four days a week ironing the official Harris logo onto the cloth.
Platman's book lays bare unexpected intricacies. Who would have guessed that the dusty shades of tweed – the greens, the browns, those washed-out blues – necessitate such bold bright yarns, shown above in all their technicolour glory? In fact, Harris yarns come in every colour of the rainbow; a dedicated colour designer then blends them according to colour "recipes", ready to be turned into the autumn shades we know and love.
And what perfectionism! Before Graham's iron is allowed anywhere near it, the tweed must be inspected: no snags, oily marks or wool discolouration is permitted. You don't stay in business for a century by taking short cuts.
'Harris Tweed: From Land to Street' by Lara Platman is published by Frances Lincoln (£25). To order a copy for the special price of £21.25 (free P&P), call Independent Books Direct on 08430 600 030, or visit www.independentbooksdirect.co.uk
Join our commenting forum
Join thought-provoking conversations, follow other Independent readers and see their replies
Comments